The utilization of the rheological and structural characteristics of polymer solutions and melts for their efficient processing
Project ID:
FK 138501
Supported by:
Hungarian National Research, Development and Innovation Office (NKFIH)
Term:
1 October 2021 - 30 September 2025
Supervisor (BME):
Dr. Kolos Molnár
Participant researchers (BME):
Dr. Ferenc Szabó
Dr. András Suplicz
Dr. Dániel Török
Dr. Ábris Dávid Virág
Project summary
The rheological behavior of polymer solutions and melts has long been of great scientific interest. The flow properties of these materials originate from the macromolecular structure (structural viscosity). Various models can be used to infer the molecular structure from the rheological behavior of the material. One of the aims of the project is to investigate the applicability of these models and validate them with actual molecular weight measurements.
The modeling of these fluids is complicated because they are highly non-Newtonian in nature, are compressible, have timedependent flow characteristics (relaxation occurs), also show a kind of shape memory, and can be stretched even in a liquid state (with tensile stresses). We see these features not as obstacles, but as factors from which we can take advantage of at the processing of thermoplastics. For example, by applying suitable shear forces, gels can be processed into nanofibers, or even self-cleaning of the sprue can be achieved at injection molding.
We plan to apply the relationships between rheological behavior and material structure, explored in this research, in three areas: continuous fibers (especially nanofibers), injection molding, and thermoplastic matrix composites. In the research, special emphasis is placed on how the processing technology itself changes the molecular weight and flowability of the raw material, as well as how we can take these into account, e.g. during simulations. It is also an interesting question how the structure of the material changes (molecular weight, crystallinity, microplastic formation) during the recycling, reprocessing, or even aging and decomposition of polymers.
Project results
Section 1
1 October 2021 - 30 September 2022
Within the framework of the project our aim is to apply the relationships between rheological behavior and material structure in 3 areas:
1. Continuous fibers
We invented a novel 3D printing method and printhead capable of 3D printing objects, which are combinations of nano-/microfibers and solid or infill layers. The method is a unique combination of fused filament fabrication and melt-blowing: the filament can be fused and then either deposited or turned into microfiber mats with the aid of hot pressurized air. We made a prototype device, and used computational fluid dynamics simulations of the airflow field, and made various tests on the generated specimens. A patent application and a journal paper was submitted.
2. Injection molding
In the first year of the project, the main rheological properties of polymers have been determined and evaluated, with particular emphasis on viscosity measurements and dynamic mechanical properties (storage modulus, loss modulus, loss factor) that can be measured in the time and/or frequency domain. Our aim was to create a generalized model that can describe the long-term relaxation behavior of polymers in a wide temperature range, i.e. for both solids and melts. The behavior during processing (injection molding) and the application are linked together. Based on the above-mentioned measurements, we established the basics of the model.
3. Thermoplastic matrix composites
We determined the limits of the processability (processing window) of the material. We have also explored several models to describe the polymerization and crystallization and viscosity change of caprolactam during the polymerization process. The Kamal-Sourour model was used to model the polymerization process. To construct the model, test specimens were prepared at 150, 170 and 190°C in the polymerization time range 0-10 min and the degree of conversion was measured. To fit the model to the measured results, a simplified Simulink model was constructed
Section 2
1 October 2022 - 30 September 2023
(1) Master curves and molecular weight
We developed a novel method that combines widely available measurement techniques, oscillatory shear rheometry, and dynamic mechanical analysis to characterize the rheological properties of thermos-rheologically simple, thermoplastic polymers over a wide frequency range, up to the glassy region. Using this method, we successfully mapped the rheological behavior of polystyrene materials from the ideally viscous to the ideally elastic state.
(2) Nano- and microfibers
As mentioned in the previous report, we built a prototype device and printhead. From the printed macroporous layers (printed grid structure) and the melt-blown microporous layers, we can build hierarchical structures with custom geometry. Fibers with a diameter of as small as 300 nm and an average of 900 ± 100 nm were generated at supersonic air velocities. We can also control the position and ratio of the fibers and the solid (or infill) parts of the printed object.
(3) Injection molding
Tests were carried out using a spiral mold and a special mold that divides the flowing melt into eight parts using T-junctions. This arrangement allows the partial separation and examination of the parts of the melt which are sheared at different degrees during the flow. Flow conditions in the molds were investigated by making partially filled parts and by pressure sensors. An optical image processing method was developed to evaluate the data.
(4) Polyamide 6 and T-RTM
We investigated the effect of technological parameters (polymerization temperature and time) on the properties of PA6 produced by anionic ring-opening polymerization. The polymerization temperature was varied between 150 and 175 °C, and the curing time was between 2 and 4 min. The mixing ratio of the components was 94% caprolactam, 3% initiator, and 3% activator—which ensures the highest conversion.
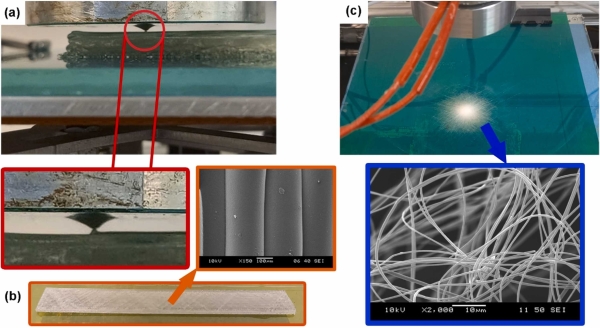
Printhead capable of making fibrous mats
Section 3
1 October 2023 - 30 September 2024
Section 4
1 October 2024 - 30 September 2025
Section 5
00 00 0000 - 00 00 0000
Project-related publications
Tóth Cs.,
Molnár K.,
Virág Á. D.: Short fiber reinforcement in material extrusion 3D printing: A meta-analysis review with insights into sustainable alternatives. Polymer Composites,
, 29850/1-29850/1-39 (2025)
https://doi.org/10.1002/pc.29850 IF=4.8 Q1
Krizsma Sz. G.,
Suplicz A.: Novel Coupled Simulation Method and Comprehensive Metrology to Enhance the Application of Prototype Injection Moulds. ,
165, 179-188 (2025)
https://doi.org/10.4028/p-q56eQa Abdullah K. K.,
Molnár K.: The influence of in vitro degradation on the properties of polylactic acid electrospun fiber mats. Fibers,
13, 1-20 (2025)
https://doi.org/10.3390/fib13010001 IF=4 Q2
Tatár B., Homlok R.,
Mészáros L.: Enhancing the shape memory performance of self-reinforced cross-linked polyethylene composites by the optimization of the production temperature. Nuclear Engineering and Technology,
57, 103617/1-103617/8 (2025)
10.1016/j.net.2025.103617 Abdullah K. K.,
Molnár K.: Current trends and future prospects of integrating electrospinning with 3D printing techniques for mimicking bone extracellular matrix scaffolds. Journal of Polymer Science,
63, 1481-1504 (2025)
https://doi.org/10.1002/pol.20241010 IF=3.9 Q2
Tatár B., Tóth E.,
Molnár K.,
Mészáros L.: Shape memory characteristics of injection molded, cross-linked all-polyethylene composites. Radiation Physics and Chemistry,
226, 112290/1-112290/9 (2025)
10.1016/j.radphyschem.2024.112290 IF=2.8 Q1
Vas L. M., Slezák E.,
Molnár K.,
Ronkay F. Gy.: Advanced avrami formula and its application to describing the isothermal crystallisation of polymers. Thermochimica Acta,
746, 179950/1-179950/19 (2025)
10.1016/j.tca.2025.179950 IF=3.1 Q2
Tóth Cs., Molnár K., Virág Á. D.: A bioműanyag termékek jövője orvostechnikai alkalmazásokban. Műanyag- és Gumiipari Évkönyv, 23, 94-100 (2025)
Krizsma Sz. G.,
Suplicz A.,
Gere D.: Customised production of injection moulded parts from recycled materials using rapid tooling approach and coupled injection moulding-thermal and mechanical simulation. Results in Engineering,
26, 105272/1-105272/15 (2025)
https://doi.org/10.1016/j.rineng.2025.105272 IF=6 D1
Párizs R. D.,
Török D.: An experimental study on the application of reinforcement learning in injection molding in the spirit of Industry 4.0. Applied Soft Computing,
167, 112236/1-112236/14 (2024)
10.1016/j.asoc.2024.112236 IF=7.2 D1
Juhász Á. Gy., Nanys M.,
Pinke B., Fadel A., Godzierz M., Juriga-Tóth K.,
Molnár K., Juriga D., Jedlovszky-Hajdú A.: Formation of three-dimensional polysuccinimide electrospun fiber meshes induced by the combination of CaCl2 and humidity. Macromolecular Rapid Communications,
, 2300625/1-2300625/12 (2024)
10.1002/marc.202300625 IF=4.2 Q2
Virág Á. D.,
Tóth Cs., Polyák P., Musioł M.,
Molnár K.: Tailoring the mechanical and rheological properties of poly(lactic acid) by sterilizing UV-C irradiation. International Journal of Biological Macromolecules,
277, 134247/1-134247/12 (2024)
https://doi.org/10.1016/j.ijbiomac.2024.134247 IF=7.7 D1
Virág Á. D.,
Juhász Zs., Kossa A.,
Molnár K.: Combining oscillatory shear rheometry and dynamic mechanical analysis to obtain wide-frequency master curves. Polymer,
295, 126742/1-126742/11 (2024)
https://doi.org/10.1016/j.polymer.2024.126742 IF=4.1 Q2
Vajtai L., Nemes N. M., del Puerto Morales M.,
Molnár K.,
Pinke B. G., Simon F.: Incidence of the Brownian Relaxation Process on the Magnetic Properties of Ferrofluids. Nanomaterials,
14, 634/1-634/15 (2024)
10.3390/nano14070634 IF=4.4 Q2
Virág Á. D.,
Tóth Cs.,
Mészáros L.,
Juhász Zs., Bezerédi Á.,
Petrény R.: Optimizing the injection molding process for thermally and electrically conductive, carbon fiber and carbon nanotube-reinforced poly(lactic acid) hybrid composites with enhanced mechanical properties. Journal of Applied Polymer Science,
141, e56148/1-e56148/11 (2024)
https://doi.org/10.1002/app.56148 IF=2.7 Q2
Virág Á. D., Molnár K.: Fertőtlenítő UV-C sugárzás politejsavra gyakorolt roncsoló hatása. Polimerek, 10, 130-136 (2024)
Krizsma Sz.,
Suplicz A.: Comprehensive Measurement and Simulation of Prototype Injection Moulds. Defect and Diffusion Forum,
435, 141-150 (2024)
10.4028/p-Y3Lvjr Tatár B.,
Mészáros L.: Shape memory characteristics of injection molded poly(lactic acid) multiscale hybrid composites. ACS Omega,
9, 46960-46967 (2024)
10.1021/acsomega.4c06592 Krizsma Sz.,
Széplaki P.,
Suplicz A.: Coupled injection moulding simulation–thermal and mechanical simulation method to analyse the operational behaviour of additively manufactured polymeric injection moulds. Results in Engineering,
23, 102558/1-102558/16 (2024)
https://doi.org/10.1016/j.rineng.2024.102558 IF=6 D1
Virág Á. D.,
Molnár K.: Modelling the time-dependent mechanical properties of thermoplastic and thermosetting polymers with Gumbel distribution functions. Polymer,
312, 127642/1-127642/12 (2024)
https://doi.org/10.1016/j.polymer.2024.127642 IF=4.1 Q2
Budavári B., Karancsi Á.,
Pinke B. G., Pállinger É., Juriga-Tóth K., Király M., Szász Zs., Voszka I.,
Molnár K., Kőhidai L., Jedlovszky-Hajdú A., S Nagy K.: Long-term shelf-life liposomes for delivery of prednisolone and budesonide. Journal of Molecular Liquids,
394, 123756/1-123756/13 (2024)
10.1016/j.molliq.2023.123756 IF=5.3 Q1
Virág Á. D.,
Suplicz A.,
Török D.: Prediction of the thermal degradation–induced colour change of acrylonitrile butadiene styrene products as a function of temperature and titanium dioxide content. Results in Engineering,
24, 103505/1-103505/11 (2024)
https://doi.org/10.1016/j.rineng.2024.103505 IF=6 D1
Széplaki P., Suplicz A.: Poliamid 6 mátrixú kompozit szendvicsszerkezetek gyárthatósága T-RTM technológiával. Polimerek, 10, 226-232 (2024)
Krizsma Sz.,
Suplicz A.: Analysis of the applicability and state monitoring of material extrusion–printed acrylonitrile butadiene styrene injection mould inserts with different infill levels. Materials Today Communications,
35, 106294/1-106294/12 (2023)
10.1016/j.mtcomm.2023.106294 IF=3.7 Q2
Virág Á. D.,
Tóth Cs.,
Molnár K.: Photodegradation of polylactic acid: Characterisation of glassy and melt behaviour as a function of molecular weight. International Journal of Biological Macromolecules,
252, 126336/1-126336/14 (2023)
10.1016/j.ijbiomac.2023.126336 IF=7.7 D1
Semperger O. V.,
Suplicz A.: The degradation during recycling of polyamide 6 produced by anionic ring‑opening polymerization of ε‑caprolactam. Scientific Reports,
13, 17130/1-17130/11 (2023)
doi.org/10.1038/s41598-023-44314-0 IF=3.8 Q1
Kara Y.,
Kovács N. K., Nagy-György P.,
Boros R.,
Molnár K.: A novel method and printhead for 3D printing combined nano-/microfiber solid structures. Additive Manufacturing,
61, 103315/1-103315/13 (2023)
10.1016/j.addma.2022.103315 IF=10.3 D1
Krizsma Sz. G.,
Suplicz A.: Comprehensive in-mould state monitoring of material jetting additively manufactured and machined aluminium injection moulds. Journal of Manufacturing Processes,
84, 1298-1309 (2022)
10.1016/j.jmapro.2022.10.070 IF=6.2 Q2
Fris D. R.,
Szabó F.: Investigation of segregation in the runner system during injection moulding. IOP Conference Series: Materials Science and Engineering,
1246, 012029/1-012029/8 (2022)
10.1088/1757-899X/1246/1/012029 Mészáros L.,
Tatár B., Toth K., Földes A., S. Nagy K., Jedlovszky-Hajdú A., Tóth T.,
Molnár K.: Novel, injection molded all-polyethylene composites for potential biomedical implant applications. Journal of Materials Research and Technology,
17, 743-755 (2022)
10.1016/j.jmrt.2022.01.051 IF=6.4 D1
Kara Y.,
Molnar K: Development of single-polypropylene composites interleaved with MWCNT-doped melt-blown fine fiber mats. Polymer Composites,
43, 5208-5221 (2022)
https://doi.org/10.1002/pc.26812 IF=5.2 Q1
Krizsma Sz. G.,
Suplicz A.: State-monitoring and product quality measurement of additively manufactured injection mould inserts. IOP Conference Series: Materials Science and Engineering,
1246, 012020/1-012020/8 (2022)
10.1088/1757-899X/1246/1/012020 Semperger O. V.,
Török D.,
Suplicz A.: Development and Analysis of an In-Mold Coating Procedure for Thermoplastic Resin Transfer Molding to Produce PA6 Composites with a Multifunctional Surface. Periodica Polytechnica-Mechanical Engineering,
66, 350-360 (2022)
10.3311/PPme.21048 IF=1.3
Kara Y.,
Molnár K.: Decomposition behavior of stereocomplex PLA melt-blown fine fiber mats in water and in compost. Journal of Polymers and the Environment,
31, 1398-1414 (2022)
10.1007/s10924-022-02694-w IF=5.3 Q1
© 2014 BME Department of Polymer Engineering - Created by: Dr. Romhány Gábor