Development of flame retarded polymer composites for engineering applications
Project ID:
K 120592
Supported by:
Hungarian National Research, Development and Innovation Office (NKFIH)
Term:
1 December 2016 - 30 November 2020
Supervisor (BME):
Prof. Dr. Tibor Czigány
Prof. Dr. Andrea Toldy
Participant researchers (BME):
Prof. Dr. Andrea Toldy
Dr. Gábor Szebényi
Dr. Péter Tamás-Bényei
Dr. Ákos Pomázi
Project summary
Nowadays in field of engineering applications the importance of fibre reinforced polymer composites as well as carbon fibre reinforced epoxy resins significantly growing due to their beneficial properties. However, the flammable polymer matrix of epoxy resin composites hinders their use in many high-tech applications. The aim of current research is the development of high-performance flame retarded composites for engineering applications (public transportation and different containers). Potential application of reactive and of additive flame retardants will be analysed, moreover optimization of manufacturing technology (hand lamination accomplished by hot-pressing method, RTM, VARTM) to avoid segregation and inhomogeneous dispersion of solid and liquid flame retardants will be carries out. Influence of reinforcement will be investigated on flame retardant dispersion as well.
Project results
Section 1
1 December 2016 - 30 November 2017
In the first year of the project literature review was carried out focusing on epoxy resin composites’ processing technologies and industrial application areas as well as flame retardancy opportunities. Based on preliminary experiments additive and reactive flame retardants, epoxy resins with low viscosity for injection and carbon fibre reinforcing materials were acquired. The physical and mechanical properties of the materials were tested. The curing process of the epoxy resins with and without additive flame retardants was be examined using differential scanning calorimetry (DSC). The optimal quantity of flame retardant additives was determined based on the influence of fire retardants on fire performance, glass transition temperature and mechanical properties. Vacuum injection equipment required for the preparation of flame retarded epoxy resin composites and 4-axis milling machine needed for composite sample preparation were acquired.
The results were published in scientific journals and conferences. Student involvement resulted in undergraduate theses, BSc and MSc diploma theses, and a PhD thesis is in progress.
Section 2
1 December 2017 - 30 November 2018
In the second year of the project experimental samples without reinforcement were produced using the previously optimized parameters. The glass transition temperature of the prepared samples was determined by differential scanning calorimetry (DSC). The thermal stability and flammability of the developed systems were studied by thermogravimetric analysis, limiting oxygen index (LOI), UL-94 standard and calorimetric methods. Composite sampled were also made by hand lamination followed by hot-pressing, resin transfer moulding (RTM) and vacuum-assisted RTM (VARTM). Analytical methods for the determination of the extent of particle filtration were reviewed and particle filtration was investigated by Raman mapping and scanning electron microscopy with energy dispersive spectroscopy (SEM-EDS) on the cross section of carbon fibre reinforced epoxy resin composites. The filtration of solid particles during composite preparation technologies based on injection presents a challenge to be solved, therefore we also overviewed the possibilities to apply the flame retardants in a separate layer on the composite. Rheological examinations were carried out to optimize the processing parameters. The results were published in scientific journals and conferences. Student involvement resulted in undergraduate theses, BSc and MSc diploma theses, and a PhD thesis is in progress.
Section 3
1 December 2018 - 30 November 2019
In the third year of the project injection tools were manufactured, and further material development and testing were carried out in agreement with the research plan. The final version of the temperable mould is a sectionable tool with a glass upper part to follow the resin flow during injection. Pressure can be measured both before the inlet and after the outlet, so that we can determine the pressure difference occurring in the manufacturing process. There is also a possibility to measure and control the resin flow before the inlet. To avoid the particle filtration, we studied the possibilities of applying the flame retardants in a separate layer on the composite. As in many application areas, gelcoats are used anyway to reach the required surface properties, a logical progression in the composite industry is the development of multifunctional gelcoats. We acquired a benchmark reference and flame retarded epoxy resin-based gelcoats, and developed our own intumescent flame retarded gelcoat formulations with 5, 10 and 15% P-content from APP. The crosslinking of the gelcoats was proved by DSC, while thermal stability was compared by TGA method. The fire performance of the gelcoats itself was compared by limited oxygen index (LOI), UL-94 and mass loss calorimetry (MLC) tests. Based on the results, the additives did not affect the crosslinking process significantly. The thermal stability and fire performance of the own formulation with 10% P content were in the same range as in the case of the benchmark flame retardant gelcoat, while the developed new formulation with 15% P content overperformed the benchmark in most cases, therefore it is a potentially patentable solution. The results were published in different scientific journals and conferences. One PhD, two MSc, two BSc and two SSC theses connected to the research were written, and one PhD thesis is in progress.
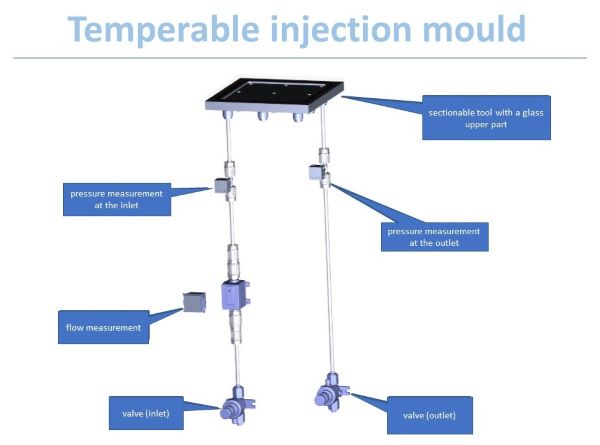
Temperable injection mould
Section 4
1 December 2019 - 30 November 2020
In the last year of the project, we applied the previously tested reference and flame retardant gelcoats to the surface of reference and flame retardant fiber-reinforced epoxy composites produced by wet compression moulding and RTM. We applied the gelcoats on the surface by brushing in a thickness of 0.5 and 1.0 mm, and then the coated composites were tested by standard flammability tests.
According to the mass loss calorimetry results of the coated samples made by wet compression moulding, non-FR gelcoats significantly impaired the fire performance of the composites, leading to high pHRR and THR, even when applied in 0.5 mm thickness. If a gelcoat layer is required on the surface of the composite part (e.g. to have appropriate surface properties), a significant increase in heat release must be taken into consideration, or a flame retarded multifunctional gelcoat should be applied. On average, the 0.5 mm thick FR gelcoats lowered the pHRR of the PER composite, which was further decreased with the addition of RDP to the composite matrix.
The 1.0 mm thick FR gelcoats lowered the pHRR of the PER composite twice as much as the 0.5 mm thick coatings on average, but the additional FR effect of the RDP was decreased at the same time. Among all composites, the FR composite coated with a gelcoat containing 15% P APP had the lowest pHRR.
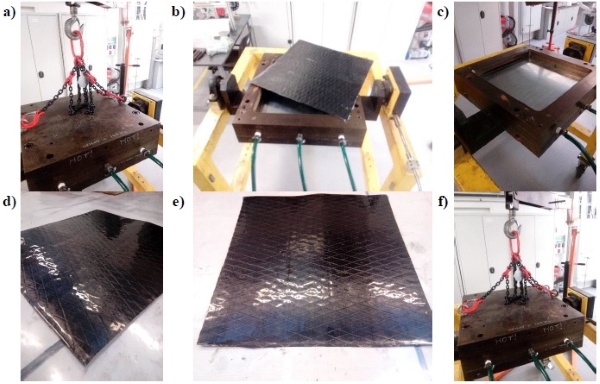
Demoulding process of composite sheet made by RTM (a) mould opening; (b) removal of the composite sheet; (c) cleaning; (d) (e) composite made by RTM; (f) closed mould ready for the next cycle
Project-related publications
Forintos N., Sarkadi T., Boros Cs. O.,
Czigány T.: Multifunctional carbon fiber sensors: The effect of anisotropic electrical conductivity. IEEE Sensors Journal,
21, 8960-8968 (2021)
10.1109/JSEN.2021.3053125 IF=4.325 Q1
Forintos N., Sarkadi T.,
Czigány T.: Electric resistance measurement–based structural health monitoring with multifunctional carbon fibers: Predicting, sensing, and measuring overload. Composites Communications,
28, 100913/1-100913/4 (2021)
10.1016/j.coco.2021.100913 IF=7.685 Q1
Pomázi Á.,
Toldy A.: Development of fire retardant epoxy-based gelcoats for carbon fibre reinforced epoxy resin composites. Progress in Organic Coatings ,
151, 106015/1-106015/12 (2021)
10.1016/j.porgcoat.2020.106015 IF=6.206 D1
Vermes B.,
Czigány T.: Non-conventional deformations: Materials and actuation. Materials,
13, 1383/1-1383/26 (2020)
10.3390/ma13061383 IF=3.623 Q1
Vermes B., Czigány T.: Alakváltó kompozitok tervezése és gyártása autoklávval. Polimerek, 6, 895-899 (2020)
Toldy A.,
Pomázi Á., Szolnoki B.: The effect of manufacturing technologies on the flame retardancy of carbon fibre reinforced epoxy resin composites. Polymer Degradation and Stability,
174, 109094/1-109094/10 (2020)
10.1016/j.polymdegradstab.2020.109094 IF=5.03 Q1
Hegedűs G.,
Czigány T.: State monitoring of polymer composites with glass optical fibre and with equipment used in telecommunication. Acta Materialia Transylvanica,
3, 1-9 (2020)
10.33924/amt-2020-01-01 Hegedűs G., Sarkadi T.,
Czigány T.: Self-sensing composite: Reinforcing fiberglass bundle for damage detection. Composites Part A: Applied Science and Manufacturing,
131, 105804/1-105804/7 (2020)
10.1016/j.compositesa.2020.105804 IF=7.664 D1
Forintos N., Czigány T.: Multifunctional carbon fiber reinforced polymer composite structures: Reinforcing and sensing. in '6th International Conference on Sensors and Electronic Instrumentation Advances Porto, Portugália. 2020.09.23-2020.09.25.,162-166 (2020)
Forintos N.,
Czigány T.: Reinforcing carbon fibers as sensors: The effect of temperature and humidity. Composites Part A: Applied Science and Manufacturing,
131, 105819/1-105819/5 (2020)
10.1016/j.compositesa.2020.105819 IF=7.664 D1
Toldy A.,
Szebényi G.,
Molnár K.,
Tóth L. F.,
Magyar B.,
Hliva V.,
Czigány T.,
Szolnoki B.: The effect of multilevel carbon reinforcements on the fire performance, conductivity, and mechanical properties of epoxy composites. Polymers,
11(2), 303/1-303/13 (2019)
10.3390/polym11020303 IF=3.426 Q1
Vas L. M., Kocsis Z.,
Czigány T., Tamás P.,
Romhány G.: Novel evaluation method of acoustic emission data based on statistical fiber bundle cells. Journal of Composite Materials,
53, 2429-2446 (2019)
10.1177/0021998319826666 IF=1.972 Q3
Pomázi Á., Toldy A.: Effect of flame retardant filtration on the fire performance of carbon fibre reinforced epoxy composites made by resin transfer moulding. in 'International Conference on Composite Materials (ICCM22) Melbourne, Australia. 2019.08.11-2019.08.16.,1-12 (2019)
Forintos N.,
Czigány T.: Multifunctional application of carbon fiber reinforced polymer composites: electrical properties of the reinforcing carbon fibers – a short review. Composites Part B: Engineering,
162, 331-343 (2019)
10.1016/j.compositesb.2018.10.098 IF=7.635 D1
Pomázi Á.,
Toldy A.: Multifunctional Gelcoats for Fiber Reinforced Composites. Coatings,
9(3), 9030173/1-9030173/23 (2019)
10.3390/coatings9030173 IF=2.436 Q2
Hegedűs G., Sarkadi T.,
Czigány T.: Multifunctional composite: Reinforcing fibreglass bundle for deformation self-sensing. Composites Science and Technology,
180, 78-85 (2019)
10.1016/j.compscitech.2019.05.018 IF=7.094 D1
Tamás-Bényei P., Bitay E., Kishi H., Matsuda S.,
Czigány T.: Toughening of Epoxy Resin: The Effect of Water Jet Milling on Worn Tire Rubber Particles. Polymers,
11, 529/1-529/11 (2019)
10.3390/polym11030529 IF=3.426 Q1
Szolnoki B.,
Toldy A.,
Marosi Gy.: Effect of Phosphorus Flame Retardants on the Flammability of Sugar-based Bioepoxy Resin. Phosphorus Sulfur and Silicon and the Related Elements,
, 1539855/1-1539855/4 (2019)
10.1080/10426507.2018.1539855 IF=1.046 Q4
Hegedűs G., Czigány T.: Sérülés helyének megállapítása kompozit szerkezetekben az üveg erősítőanyag felhasználásával. in 'XXVII. Nemzetközi Gépészeti Konferencia OGÉT 2019 Nagyvárad. 2019.04.25-2019.04.28.,189-192 (2019)
Vermes B., Czigány T.: Layup optimization and ways to improve the manufacturability of coupled composites. in 'International Conference on Composite Materials (ICCM22) Melbourne, Australia. 2019.08.11-2019.08.16,7 (2019)
Hegedűs G., Sarkadi T.,
Czigány T.: Self-sensing polymer composite: white-light-illuminated reinforcing fibreglass bundle for deformation monitoring. Sensors,
19, 1745/1-1745/8 (2019)
10.3390/s19071745 IF=3.275 Q1
Toldy A., Pomázi Á., Szolnoki B.: The effect of manufacturing technologies on the flame retardancy of carbon fibre reinforced epoxy resin composites. in 'European Meeting on Fire Retardancy and Protection of Materials (FRPM19) Turku, Finland. 2019.06.26-28.,2 (2019)
Pomázi Á., Toldy A.: Égésgátolt glicerin alapú epoxigyanta kompozitok fejlesztése mérnöki alkalmazásokhoz. Polimerek, 4(2), 59-64 (2018)
Marosi Gy., Hirsch E.,
Bocz K.,
Toldy A.,
Szolnoki B.,
Bodzay B., Csontos I., Farkas A., Balogh A., Démuth B., Nagy Z., Pataki H.: Pharmaceutical and macromolecular technologies in the spirit of industry 4.0. Periodica Polytechnica-Chemical Engineering,
64, 4 (2018)
10.3311/PPch.12870 IF=1.382 Q3
Hegedűs G., Czigány T.: Polimer kompozit termékek komplexitását kihasználó üvegszálas érzékelő csatlakozójának fejlesztése. in 'OGÉT 2018: XXVI. Nemzetközi Gépészeti Konferencia Marosvásárhely, Románia. 2018.04.26-2018.04.29.,179-182 (2018)
Pomázi Á.,
Toldy A., Szolnoki B.: Flame Retardancy of Low-Viscosity Epoxy Resins and Their Carbon Fibre Reinforced Composites via a Combined Solid and Gas Phase Mechanism. Polymers,
10, 1081/1-1081/13 (2018)
doi:10.3390/polym10101081 IF=3.164 Q1
Toldy A.: Editorial corner - a personal view Flame retardancy of carbon fibre reinforced composites.
Vermes B., Czigány T.: Kompozitok alakváltásának lehetőségei. Gép, 69, 51-54 (2018)
Hegedűs G.,
Czigány T.: Developing a glass fibre sensor for polymer technology applications. IOP Conference Series: Materials Science and Engineering,
426, 012015/1-012015/1-4 (2018)
10.1088/1757-899X/426/1/012015 Toldy A.,
Niedermann P.,
Pomazi A., Marosi G., Szolnoki B.: Flame Retardancy of Carbon Fibre Reinforced Sorbitol Based Bioepoxy Composites with Phosphorus-Containing Additives. Materials,
10, 467/1-467/ (2017)
10.3390/ma10050467 IF=2.467 Q2
Péter B., Hegedűs G., Czigány T.: T-RTM eljárással gyártott alkatrészek gyártási folyamatának kihívásai, különös tekintettel az erősítőanyagok kezelésére. Gép, 68, 37-42 (2017)
Hegedűs G., Czigány T.: Optikai szálak alkalmazása polimer anyagvizsgálatokhoz. in 'OGÉT 2017: XXV. Nemzetközi Gépészeti Konferencia Kolozsvár, Románia. 2017.04.27-2017.04.30.,175-178 (2017)
Hegedűs G., Sarkadi T.,
Czigány T.: Analysis of the light transmission ability of reinforcing glass fibers used in polymer composites. Materials,
10(6), 637/1-9 (2017)
10.3390/ma10060637 IF=2.467 Q2
Pomazi A.,
Toldy A.: Particle Distribution of Solid Flame Retardants in Infusion Moulded Composites. Polymers,
9, 250/1-250/ (2017)
10.3390/polym9070250 IF=2.935 Q1
Czigány T., Forintos N., Hegedűs G.: Health monitoring of high-performance polymer composites with multifunctional fibers. in 'ICCM21 Xi'an, Kína. 2017.08.20-2017.08.25.,8 (2017)
© 2014 BME Department of Polymer Engineering - Created by: Dr. Romhány Gábor