Investigation of additive manufactured 3D reinforcing framework structure as insert in injection molded composite products
Project ID:
FK 134336
Supported by:
Hungarian National Research, Development and Innovation Office (NKFIH)
Term:
1 September 2020 - 31 August 2024
Supervisor (BME):
Dr. Tamás Tábi
Participant researchers (BME):
Dr. Norbert Krisztián Kovács
Dr. András Suplicz
Dr. Ferenc Szabó
Project summary
Nowadays polymer products are more and more often used in parts of critical safety and parts subjected to high loads. As a result, fiber-reinforced composites receive more and more attention. Their mechanical properties are anisotropic, and depend on the orientation of the reinforcement.
Fiber-reinforced materials can be injection molded; here the orientation of the fibers is basically determined by the flow conditions. As a result, the part often needs to have increased wall thickness or reinforcing ribs to satisfy mechanical requirements. Ribs, however, mean extra material, weight and cost. Another problem is the weld lines, which result in the forming of mechanically critical areas. A further problem is fiber breaking, caused by the technology.
The goal of the project is to create a complex design methodology with which a tailor-made reinforcing structure can be made in injection molded parts as a separate step, by 3D printing. Its advantage is that the characteristics of the reinforcing structure (orientation, fiber content etc.) can be made independent of flow conditions and can be changed in each point according to the load. Another advantage of the procedure is that fiber shortening can also be greatly reduced, thus the reinforcing effect is increased and recyclability by remelting is better facilitated. A further goal is to apply and extend the developed method for biopolymers like Poly(Lactic Acid) (PLA), the one which is mostly in focus for biopolymer research.
Project results
Section 1
1 September 2020 - 31 August 2021
In the first research period, the first task was to review the literature of biopolymers and reinforced biopolymer composites (biocomposites). We focused on to explore the available techniques to hinder the mentioned drawback of PLA and thus to improve HDT and impact strength. The possibilities of improving ductility of PLA was reviewed like using plasticizers, impact modifiers or using another, inherently tough biopolymer as a second phase in a blend with PLA. By summarizing the literature, a review paper was published in the Q1 ranked Polymer Testing journal. Parallel to the literature review, we started to purchase the raw materials, the Devo filament extruder and fiber production equipment for producing the composite filaments, and a Markforged Method X type FFF device with a heated workspace. The research was continued by the measurement of the necessary material properties for the coupled thermal-mechanical finite element tests. Injection molding simulations were used to model the production technology, to examine the geometries for manufacturability, and to calculate the loads on the structure calculated from the injection molding simulations. Finally, we focused on the practical experiments to investigate the processability of PLA and basalt fiber composites by 3D printing. Following the fabrication of the composite filaments, specimens were fabricated and microstructural studies were performed to determine the fiber length distribution, orientation, and porosity of the printed structures. It was found that in the unreinforced PLA specimen, characteristic triangular air gaps are formed between two fibers along the printing direction, and the amount of these triangular air gaps is reduced by using fiber reinforcement. Based on our studies, this fiber length is below the critical fiber length value, so our further research tasks include increasing the residual fiber length of composites using gentler processing.
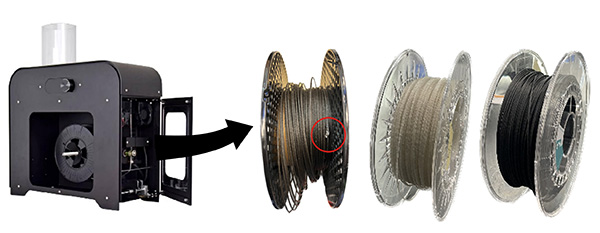
PLA and PLA based basalt composite filamanet production
Section 2
1 September 2021 - 31 August 2022
We aimed to increase residual fiber length by developing a novel manufacturing process not yet applied to fiber manufacturing. Unfilled PLA feedstock was fed into the twin-screw extruder and the continuous basalt fiber roving was introduced through the venting orifice close to the die, thus minimizing the shear stress on the fibers. Average fiber length increased from 60 µm for cut fibers to 1.3 mm (1300 µm). We investigated the expected mechanical properties of short-fiber composites and the applicability of the predictive methods to printed structures. We found that existing calculation methods that are well applicable to injection molded composites are often inaccurate for 3D printed composites, and thus require further correction and supplementation. Another task was the design and fabrication of custom 3D printed insert geometries for subsequent injection molding experiments. We finally selected 4 inserts for the 3D printing tests. We performed preliminary injection molding tests of lubricant-filled PLA in a standard tensile test mold without a skeleton. We examined the resulting deformations in an injection mold with a glass insert and analyzed the images using digital image correlation. Finite element calculations were performed in the ANSYS software. We calculated the forces originating from the flow, which were used as input data for the mechanical calculations, in a Moldex3D environment. To overcome issues with high viscosity, Calcium Stearate (Ca-ST) was chosen as lubricant. We found that with 1m% Ca-ST, the flow rate of the PLA used increased significantly. Based on this, it was possible to simplify the impregnation process of the skeleton structure. At the same time, we also continued to develop the thermal dimensional stability of the PLA matrix material. With in-mold crystallization and the use of efficient nucleating agents, the heat deflection temperature of the injection molded PLA specimens increased from 55°C to more than 120°C.
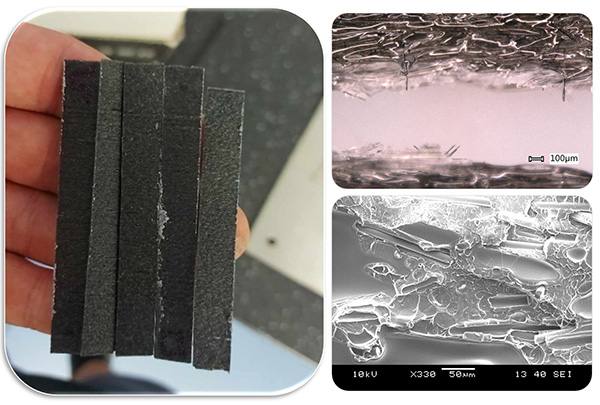
3D printed composite structure
Section 3
1 September 2022 - 31 August 2023
In the third year, we continued our research on PLA. We investigated the different additives, pore formers and the migration of plasticisers to the surface of the product. We found that, contrary to preliminary expectations, there was less diffusion of additives from crystallised PLA test specimens. We also tested three-phase bioplastic mixtures in which all three phases were biopolymers (PLA, PBAT and PBS (PolyButylene Succinate)). Both PBAT and PBS were shown to have a crystal-forming effect, and their use increased the elongation at break of PLA very significantly (from 3.7% to more than 20%). In the rest of our research, we focused on fibre-reinforced skeletal structures to be created by 3D printing. Based on the results of the preliminary experiments, we printed 10x10x10 mm gyroid unit cells with different nozzle diameters and verified their dimensional accuracy using an optical microscope. It was found that the dimensional accuracy of the applied gyroid unit cell geometry was most accurate for nozzle diameters of 0.4 mm. The mechanical properties of the cells were qualified by compression tests. The gyroid specimens exhibit the typical plateau of the cells, being able to withstand large deformation at a nearly constant stress, which in this case is 20-25 MPa/g. Subsequently, the gyroid structure was used as an insulator for injection moulding. The injection moulding parameters required for the complete filling around the 3D printed inserts were determined. Subsequently, a compression test was also performed on the injection moulded samples. For the injection moulded specimens, the linear elastic and the plateau phase cannot be separated as sharply as for the inert specimens. This is due to the multiphase structure. It was found that the plateau section is not preceded by a stress drop, so the designed inert geometry has its effect. Overall, the injection moulding experiments were successful.
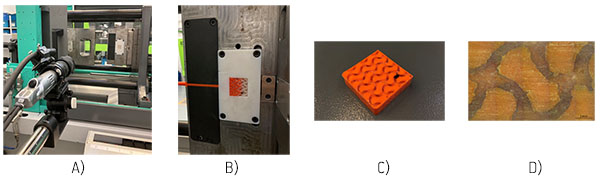
Injection moulding test: A: measurement setup; B: short shut; C: fully completed / filled product; D: cross sectional view of the moulded piece
Section 4
1 September 2023 - 31 August 2024
Project-related publications
Krizsma Sz.,
Mészáros L.,
Kovács N. K.,
Suplicz A.: Expanding the applicability of material jetting–printed photopolymer prototype injection moulds by gamma irradiation post-treatment. Journal of Manufacturing Processes,
134, 135-145 (2025)
https://doi.org/10.1016/j.jmapro.2024.12.037 IF=6.1 Q1
Csézi G.,
Tábi T.: Mechanical and morphological properties of uniaxially oriented and heat-treated poly(lactic acid)/poly(butylene adipate-co-terephthalate) blends. Advances in Polymer Technology,
, 7082244/1-7082244/11 (2025)
10.1155/adv/7082244 IF=2 Q3
Tóth Cs.,
Virág Á. D.,
Vas L. M.,
Kovács N. K.: Prediction and analysis of flexural stiffness for 3D-printed continuous fiber–reinforced composites with different matrix fill ratios and layer orders. Polymer Testing,
135, 108459/1-108459/11 (2024)
https://doi.org/10.1016/j.polymertesting.2024.108459 IF=5 D1
Párizs R. D.,
Török D.: An experimental study on the application of reinforcement learning in injection molding in the spirit of Industry 4.0. Applied Soft Computing,
167, 112236/1-112236/14 (2024)
10.1016/j.asoc.2024.112236 IF=7.2 D1
Tóth Cs.,
Lukács N. L.,
Kovács N. K.: The role of the fiber–matrix interface in the tensile properties of short fiber–reinforced 3D-printed polylactic acid composites. Polymer Composites,
45, 13589-13602 (2024)
https://doi.org/10.1002/pc.28720 IF=4.8 Q1
Szederkényi B., Rácz I.,
Kovács N.K.,
Czigány T.: Finite element modelling of continuous fiber–reinforced composites produced by automated manufacturing. IOP Conference Series: Materials Science and Engineering,
1313, 012002/1-012002/8 (2024)
10.1088/1757-899X/1313/1/012002 Tábi T.,
Gere D.,
Csézi G.,
Pölöskei K.: Influence of Epoxidized Natural Rubber of the thermoformability of Poly(Lactic Acid) biopolymer films using elevated temperature ball burst tests. Journal of Thermal Analysis and Calorimetry,
149, 75-87 (2024)
10.1007/s10973-023-12712-1 IF=3 Q2
Dragan V. K., Petrovics N., Kirchkeszner Cs.,
Tábi T., Szabó B. S., Eke Zs.: The kinetics of swelling and migration: A case study of plasticized polylactic acid food contact plastics tested with ethanolic food simulants. Express Polymer Letters,
18, 391-405 (2024)
10.3144/expresspolymlett.2024.29 IF=2.7 Q2
Krizsma Sz.,
Széplaki P.,
Suplicz A.: Coupled injection moulding simulation–thermal and mechanical simulation method to analyse the operational behaviour of additively manufactured polymeric injection moulds. Results in Engineering,
23, 102558/1-102558/16 (2024)
https://doi.org/10.1016/j.rineng.2024.102558 IF=6 D1
Tóth Cs.,
Vas L. M.,
Kovács N. K.: Achieving gradual failure under bending by the layering design of 3D printed continuous fiber reinforced composites. Results in Engineering,
22, 102075/1-102075/8 (2024)
https://doi.org/10.1016/j.rineng.2024.102075 IF=6 D1
Szederkényi B., Czigány T., Kovács N. K.: Investigation of continuous fiber–reinforced triply periodic minimal surfaces (TPMS) for high-performance energy absorption applications. in 'ECCM21 – 21st European Conference on Composite Materials Nantes, Franciaország. 2024.06.02-2024.06.05.,1651-1658 (2024)
Széplaki P., Szabó F.: Fröccsöntő szerszám inzertek deformációinak mérése és vizsgálata gyártási ciklus közben. in 'OGÉT 2023 : XXXI. Nemzetközi Gépészeti Konferencia Temesvár, Románia. 2023.04.27- 2023.04.30,450-453 (2023)
Kotrocz L.,
Bakonyi P.: Investigation the temperature-dependent surface mechanical properties of PolyJet printed samples by cyclic indentation testing in a DMA system. Results in Materials,
17, 100360/1-100360/8 (2023)
10.1016/j.rinma.2022.100360 Csézi G., Tábi T.: Hőkezelési hőmérséklet hatása a nyújtott politejsav tulajdonságaira. in 'XXXI. Nemzetközi Gépészeti Konferencia (OGÉT 2023) Temesvár, Románia. 2023.04.27-2023.04.30.,75-80 (2023)
Krizsma Sz. G.,
Suplicz A.: Monitoring and modelling the deformation of an aluminium prototype mould insert under different injection moulding and clamping conditions. Results in Engineering,
20, 101556/1-101556/13 (2023)
10.1016/j.rineng.2023.101556 IF=6 D1
Petrovics N., Kirchkeszner Cs., Patkó A.,
Tábi T., Magyar N., Kovácsné Székely I., Szabó B. S., Nyiri Z., Eke Zs.: Effect of crystallinity on the migration of plastic additives from polylactic acid-based food contact plastics. Food Packaging and Shelf Life,
36, 101054/1-101054/11 (2023)
10.1016/j.fpsl.2023.101054 IF=8.5 D1
Krizsma Sz.,
Suplicz A.: Analysis of the applicability and state monitoring of material extrusion–printed acrylonitrile butadiene styrene injection mould inserts with different infill levels. Materials Today Communications,
35, 106294/1-106294/12 (2023)
10.1016/j.mtcomm.2023.106294 IF=3.7 Q2
Kara Y.,
Kovács N. K., Nagy-György P.,
Boros R.,
Molnár K.: A novel method and printhead for 3D printing combined nano-/microfiber solid structures. Additive Manufacturing,
61, 103315/1-103315/13 (2023)
10.1016/j.addma.2022.103315 IF=10.3 D1
Hajagos Sz., Zink B.: Polimer fröccsöntő inzertek deformációs viselkedésének modellezése numerikus számításokkal. in 'XXXI. Nemzetközi Gépészeti Konferencia OGÉT Temesvár, Románia. 2023.04.27-2023.04.30.,183-188 (2023)
Krizsma Sz., Suplicz A.: Prototípus fröccsöntő szerszámok üzem közbeni állapotfelügyelete és termékminőség vizsgálata. in 'XXXI. Nemzetközi Gépészeti Konferencia Temesvár, Románia. 2023.04.17-2023.04.30.,323-328 (2023)
Kiss B., Párizs R. D., Tóth Cs., Török D., Kovács N. K.: Anyagextrúzió alapú additív gyártástechnológiával készült termékek anizotróp viselkedésének elemzése. Polimerek, 5, 155-160 (2023)
Tábi T.: Háromfázisú bioműanyag keverékek vizsgálata. in 'XXXI. Nemzetközi Gépészeti Konferencia (OGÉT 2023) Temesvár, Románia. 2023.04.27-2023.04.30.,460-465 (2023)
Semperger O. V.,
Suplicz A.: The effect of the titanium dioxide nanoparticles on the morphology and degradation of polyamide 6 prepared by anionic ring-opening polymerization. Polymer Engineering and Science,
62, 2079-2088 (2022)
10.1002/pen.25990 IF=3.2 Q2
Petrény R.,
Tóth Cs.,
Mészáros L., Horváth A.: Development of electrically conductive hybrid composites with a poly(lactic acid) matrix, with enhanced toughness for injection molding, and material extrusion-based additive manufacturing. Heliyon,
8, e10287/1-e10287/8 (2022)
10.1016/j.heliyon.2022.e10287 IF=4 Q2
Tábi T.,
Ageyeva T.,
Kovács J. G.: The influence of nucleating agents, plasticizers, and molding conditions on the properties of injection molded PLA products. Materials Today Communications,
32, 103936/1-103936/8 (2022)
10.1016/j.mtcomm.2022.103936 IF=3.8 Q2
Petrovics N., Kirchkeszner Cs.,
Tábi T., Magyar N., Kovácsné Székely I., Szabó B. S., Nyiri Z., Eke Zs.: Effect of temperature and plasticizer content of polypropylene and polylactic acid on migration kinetics into isooctane and 95 v/v% ethanol as alternative fatty food simulants. Food Packaging and Shelf Life,
33, 100916/1-100916/10 (2022)
10.1016/j.fpsl.2022.100916 IF=8 D1
Tábi T.,
Pölöskei K.: The effect of processing parameters and Calcium-stearate on the ejection process of injection molded Poly(Lactic Acid) products. Periodica Polytechnica-Mechanical Engineering,
66, 17-25 (2022)
10.3311/PPme.18246 IF=1.3
Ageyeva T.,
Kovács J. G.,
Tábi T.: Comparison of the efficiency of the most effective heterogeneous nucleating agents for Poly(lactic acid). Journal of Thermal Analysis and Calorimetry,
147, 8199-8211 (2022)
10.1007/s10973-021-11145-y IF=4.4 Q1
Krizsma Sz. G.,
Suplicz A.: State-monitoring and product quality measurement of additively manufactured injection mould inserts. IOP Conference Series: Materials Science and Engineering,
1246, 012020/1-012020/8 (2022)
10.1088/1757-899X/1246/1/012020 Párizs R. D.,
Török D.,
Ageyeva T.,
Kovács J. G.: Machine learning in injection molding: An industry 4.0 method of quality prediction. Sensors,
22, 2704/1-2704/16 (2022)
10.3390/s22072704 IF=3.9 Q2
Tóth Cs.,
Kovács N. K.: Comparison of the accuracy of analytical models for basalt fiber–reinforced poly(lactic acid) composites prepared by injection molding and fused filament fabrication. International Journal of Advanced Manufacturing Technology,
121, 3999–4010 (2022)
10.1007/s00170-022-09572-8 IF=3.4 Q2
Tábi T.: Talkum hatása a politejsav biopolimer tulajdonságaira. in 'XXX. Nemzetközi Gépészeti Konferencia (OGÉT 2022) Székelyudvarhely, Románia. 2022.04.21-2022.04.24.,5 (2022)
Krizsma Sz. G.,
Suplicz A.: Comprehensive in-mould state monitoring of material jetting additively manufactured and machined aluminium injection moulds. Journal of Manufacturing Processes,
84, 1298-1309 (2022)
10.1016/j.jmapro.2022.10.070 IF=6.2 Q2
Tóth Cs.,
Kovács N. K.: Development of a Novel Hybrid Manufacturing Technology For Continuous Fiber-Reinforced Thermo-Plastic Composites. Acta Materialia Transylvanica,
5, 39-44 (2022)
10.33924/amt-2022-01-09 Csézi G., Tábi T.: Orientált biopolimer szerkezetek vizsgálata. in 'XXIX. Nemzetközi Gépészeti Konferencia (OGÉT 2021) Románia. 2021.04.23.,101-105 (2021)
Tábi T.: Tények és tévhitek a biopolimerekkel kapcsolatban - II. rész (másodközlés). Polimerek, 7, 337-340 (2021)
Krizsma Sz. G.,
Kovács N. K.,
Kovács J. G.,
Suplicz A.: In-situ monitoring of deformation in rapid prototyped injection molds. Additive Manufacturing,
42, 102001/1-102001/8 (2021)
10.1016/j.addma.2021.102001 IF=11.632 D1
Tábi T.,
Ageyeva T.,
Kovács J. G.: Improving the ductility and heat deflection temperature of injection molded Poly(lactic acid) products: A comprehensive review. Polymer Testing,
101, 107282/1-107282/36 (2021)
10.1016/j.polymertesting.2021.107282 IF=4.931 D1
Széplaki P., Hajagos Sz., Zink B., Szabó F.: Fröccsöntött termékben elhelyezett fotopolimer inzert hőtanának és deformációjának vizsgálata. in 'XXIX. Nemzetközi Gépészeti Konferencia OGÉT Online. 2021.04.23.,196-199 (2021)
Szabó F.,
Suplicz A.,
Kovács J. G.: Development of injection molding simulation algorithms that take into account segregation. Powder Technology,
389, 368-375 (2021)
10.1016/j.powtec.2021.05.053 IF=5.64 Q1
Semperger O. V., Pomlényi P., Suplicz A.: Felület-bevonatolási eljárás T-RTM technológiához. Polimerek, 7, 186-192 (2021)
Krizsma Sz. G., Suplicz A.: Additív gyártástechnológiával előállított fröccsöntő szerszámbetétek üzem közbeni deformációinak vizsgálata. Polimerek, 7, 155-160 (2021)
Kirchkeszner Cs., Petrovics N.,
Tábi T., Magyar N., Kovács J., Szabó B. S., Nyiri Z., Eke Zs.: Swelling as a promoter of migration of plastic additives in the interaction of fatty food simulants with polylactic acid- and polypropylene-based plastics. Food Control,
132, 108354/1-108354/12 (2021)
10.1016/j.foodcont.2021.108354 IF=6.652 Q1
Tábi T.: Fröccsöntött politejsav biopolimer sorozatgyárthatóságának elemzése. in 'XXIX. Nemzetközi Gépészeti Konferencia (OGÉT 2021) Románia. 2021.04.23.,200-203 (2021)
Tábi T.: Tények és tévhitek a biopolimerekkel kapcsolatban - I. rész (másodközlés). Polimerek, 7, 298-301 (2021)
Tábi T.: Tények és tévhitek a biopolimerekkel kapcsolatban - II. rész. Biohulladék, 14, 21-26 (2021)
© 2014 BME Department of Polymer Engineering - Created by: Dr. Romhány Gábor