Development of novel carbon fiber reinforcement structures for the designable reinforcement of mass-produced polymer composite products
Project ID:
2018-1.3.1-VKE-2018-00001
Supported by:
Hungarian National Research, Development and Innovation Office (NKFIH)
Term:
1 May 2019 - 30 April 2022
Supervisor (BME):
Dr. József Gábor Kovács
Dr. András Suplicz
Consortium partners (BME):
Zoltek Zrt. (konzorciumvezető)
Project summary
The project aims to develop carbon fiber composite technologies that present affordable and
lightweight solutions for mass produced cars. With these products, automotive parts can be
lighter and therefore less energy is used when the cars are manufactured and used. One technology that we intend to develop further is the
sheet molding compound (SMC) procedure. Its main advantage is that there is less waste during manufacturing than in the case of
conventional long-fiber composite technologies (RTM, Prepreg). This technology will be developed and its disadvantage eliminated so that
there will be controlled fiber orientation, and therefore plannable load-bearing in the structure. Another technology that we intend to develop
further is thermoplastic resin infusion, which can eliminate the disadvantages of cross-linked base materials, and combines the excellent
impregnation capability of cross-linked systems and the versatile processability and recyclability of thermoplastic systems. Development here
also focuses on the simpler and more cost-effective achievement of the planned orientation. The project therefore offers alternative solutions
for the more effective utilization of available energy and material resources, as it is likely that in the near future, before 2025, demand will grow
considerably for light and strong structural materials. The goal of the project is to insert the PX35 carbon fiber roving (which has a high value
for money, as a textile-type precursor-based carbon fiber, with a production capacity increase of 6 months, in contrast to competitors' 18-24
months of implementation, stable long-term sustainable pricing.) manufactured by Zoltek Zrt. in an oriented way in the case of SMC and
thermoplastic resin infusion, to utilize its advantageous properties to the fullest. The SMC technology, although it is cost effective, currently
produces considerable worse mechanical properties than long-fiber composite technologies. Thermoplastic resin infusion in its present state
produces excellent mechanical and recycling properties, but it is not competitive at present because of the uncertainty of preform
manufacturing and the technology. The suggested new hybrid SMC technology and hybrid thermoplastic resin infusion, however, provides a
competitive advantage to Zoltek Zrt. with which they can produce and sell to the car industry considerably more (up to 50%) carbon fiber
(PX35). Technologies to be developed in the project in public transport, shipbuilding, product shipment, and sports equipment – in all areas
where the light weight is a benefit – but also in household appliances and robotics. The novelty of the project is – in addition to oriented
reinforcement – better adhesion between the 50K rovings and matrix materials, which leads to even higher strength in the products. For the
development project, Zoltek will use the new layup strategy (called KASSEN) of its PX35 carbon fibers, which will improve manufacturing. The
success of the project is ensured by the many years of experience of Zoltek Zrt. in manufacturing carbon fibers and developing their
manufacturing technology, and the results achieved by the Department of Polymer Engineering of BME in research, development and
innovation, and its research background. This is further reinforced by the cooperation agreement between the company and the Department,
as a result of which, there has been several years of cooperation in areas of basic science.
Project results
Section 1
1 May 2019 - 30 April 2020
In the reporting period, we have established our knowledge in the field of caprolactam processing by a comprehensive literature search at the Department of Polymer Engineering at BME. We have shown which activators and catalysts are needed for caprolactam and in which amounts to allow the polymerization process to take place. It is advantageous to carry out the polymerization below the Tm temperature (140-160 °C), because high conversion and high crystalline fraction can be achieved and a solid polymer is obtained at the end of the polymerization. In addition, the T-RTM technology process and the equipment that can be used for it (literature and patent search) were presented. The main features of SMC technology and the manufacturing possibilities of 3D reinforcement structures were presented. In our experimental work, we investigated the ring-opening polymerization process of ε-caprolactam and the influence of different factors on the anionic polymerization and the properties of the final polymer. The prepared samples were subjected to mechanical, thermal and rheological tests. It has been shown that ambient humidity inhibits the polymerization process and has a plasticizing effect on the final polyamide. Using rheometric measurements, we have demonstrated that the reaction accelerates with increasing polymerization temperature, leading to a significant increase in the viscosity of the material. Thus, the limits of the processability (processing window) of the material were demonstrated. Several models have been presented to describe the polymerization and crystallization, and viscosity change processes of caprolactam. These models can be used in our future simulation developments.
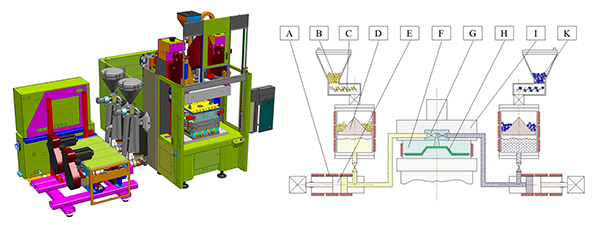
T-RTM machine: A – heating; B – ε-CL+initiator; C – dosing unit; D – melting unit; E – dosing unit; F – mold; G – mixing head; H – product; I – clamping unit; K – ε-CL+activator
Section 2
1 May 2020 - 30 April 2021
During this milestone, we designed and fabricated several experimental reinforcement structures to increase the strength and modulus of the samples. The reinforcing structures were fabricated using a Markforged 3D printer from fibre-reinforced polyamide material. The embedding experiments were carried out by injection moulding in the first instance. As a result, we obtained that the structures resulted in a 30% increase in the tested mechanical properties. Next, the embeddability during in-situ polymerization of polyamide 6 with anionic ring-opening was investigated. The polymerization experiments were successful, with good adhesion between the structure and the matrix. It was also shown that if the preform is not dried, its moisture content inhibits the polymerization process. We also measured the permeability of several fabrics used for composites, which provide important material properties for simulation analyses. By modifying the settings and material properties of conventional RTM simulations, we were able to model the T-RTM process. Several material models were developed for this purpose. We also designed a T-RTM mold to produce samples on the equipment.
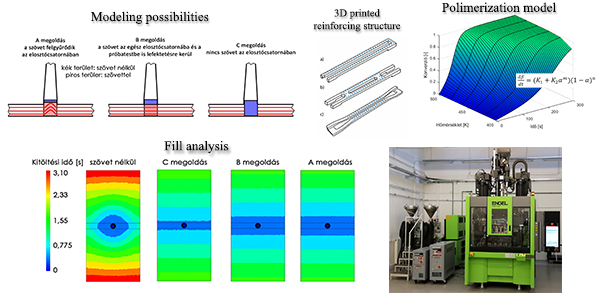
Section 3
1 May 2021 - 30 April 2022
Project-related publications
Horváth Sz.,
Kovács J. G.: Effect of processing parameters and wall thickness on the strength of injection molded products. Periodica Polytechnica-Mechanical Engineering,
68, 78-84 (2024)
10.3311/PPme.24068 IF=1.3 Q3
Kotrocz L.,
Bakonyi P.: Investigation the temperature-dependent surface mechanical properties of PolyJet printed samples by cyclic indentation testing in a DMA system. Results in Materials,
17, 100360/1-100360/8 (2023)
10.1016/j.rinma.2022.100360 Párizs R. D.,
Török D.,
Ageyeva T.,
Kovács J. G.: Multiple in-mold sensors for quality and process control in injection molding. Sensors,
23, 1735/1-1735/18 (2023)
10.3390/s23031735 IF=3.4 Q2
Szuchács A.,
Ageyeva T.,
Kovács J. G.: Modeling and measuring the bonding strength of overmolded polymer parts. Polymer Testing,
125, 108133/1-108133/15 (2023)
10.1016/j.polymertesting.2023.108133 IF=5 D1
Török D.,
Ageyeva T.,
Boros R., Kovács Á.,
Kovács J. G.: Developing a method for evaluating color changeover in a hot-runner multi-cavity injection mold. Polymer Testing,
115, 107759/1-107759/9 (2022)
10.1016/j.polymertesting.2022.107759 IF=5.1 D1
Boros R.,
Ageyeva T., Golcs Á., Krafcsik O. H.,
Kovács J. G.: Plasma treatment to improve the adhesion between ABS and PA6 in hybrid structures produced by injection overmolding. Polymer Testing,
106, 107446/1-107446/11 (2022)
10.1016/j.polymertesting.2021.107446 IF=5.1 D1
Semperger O. V.,
Török D.,
Suplicz A.: Development and Analysis of an In-Mold Coating Procedure for Thermoplastic Resin Transfer Molding to Produce PA6 Composites with a Multifunctional Surface. Periodica Polytechnica-Mechanical Engineering,
66, 350-360 (2022)
10.3311/PPme.21048 IF=1.3
Török D.,
Zink B.,
Ageyeva T., Hatos I., Zobač M., Fekete I.,
Boros R., Hargitai H.,
Kovács J. G.: Laser powder bed fusion and casting for an advanced hybrid prototype mold. Journal of Manufacturing Processes,
81, 748-758 (2022)
10.1016/j.jmapro.2022.07.034 IF=6.2 Q2
Zink B.,
Kovács J. G.: Pressure‐dependent heat transfer coefficient measurement for thermoplastic melts. Polymer Engineering and Science,
62, 1137-1146 (2022)
10.1002/pen.25912 IF=3.2 Q2
Krizsma Sz. G.,
Suplicz A.: Comprehensive in-mould state monitoring of material jetting additively manufactured and machined aluminium injection moulds. Journal of Manufacturing Processes,
84, 1298-1309 (2022)
10.1016/j.jmapro.2022.10.070 IF=6.2 Q2
Tóth Cs.,
Kovács N. K.: Comparison of the accuracy of analytical models for basalt fiber–reinforced poly(lactic acid) composites prepared by injection molding and fused filament fabrication. International Journal of Advanced Manufacturing Technology,
121, 3999–4010 (2022)
10.1007/s00170-022-09572-8 IF=3.4 Q2
Párizs R. D.,
Török D.,
Ageyeva T.,
Kovács J. G.: Machine learning in injection molding: An industry 4.0 method of quality prediction. Sensors,
22, 2704/1-2704/16 (2022)
10.3390/s22072704 IF=3.9 Q2
Petrény R.,
Tóth Cs.,
Mészáros L., Horváth A.: Development of electrically conductive hybrid composites with a poly(lactic acid) matrix, with enhanced toughness for injection molding, and material extrusion-based additive manufacturing. Heliyon,
8, e10287/1-e10287/8 (2022)
10.1016/j.heliyon.2022.e10287 IF=4 Q2
Semperger O. V.,
Suplicz A.: The effect of the titanium dioxide nanoparticles on the morphology and degradation of polyamide 6 prepared by anionic ring-opening polymerization. Polymer Engineering and Science,
62, 2079-2088 (2022)
10.1002/pen.25990 IF=3.2 Q2
Krizsma Sz. G.,
Suplicz A.: State-monitoring and product quality measurement of additively manufactured injection mould inserts. IOP Conference Series: Materials Science and Engineering,
1246, 012020/1-012020/8 (2022)
10.1088/1757-899X/1246/1/012020 Szabó F.,
Suplicz A.,
Kovács J. G.: Development of injection molding simulation algorithms that take into account segregation. Powder Technology,
389, 368-375 (2021)
10.1016/j.powtec.2021.05.053 IF=5.64 Q1
Krizsma Sz. G., Suplicz A.: Additív gyártástechnológiával előállított fröccsöntő szerszámbetétek üzem közbeni deformációinak vizsgálata. Polimerek, 7, 155-160 (2021)
Semperger O. V., Pomlényi P., Suplicz A.: Felület-bevonatolási eljárás T-RTM technológiához. Polimerek, 7, 186-192 (2021)
Rajamani P. K.,
Ageyeva T.,
Kovács J. G.: Personalized mass production by hybridization of additive manufacturing and injection molding. Polymers,
13, 309/1-309/19 (2021)
10.3390/polym13020309 IF=4.967 Q1
Szuchács A.,
Ageyeva T.,
Boros R.,
Kovács J. G.: Bonding strength calculation in multicomponent plastic processing technologies. Materials And Manufacturing Processes,
36, 151-159 (2021)
10.1080/10426914.2021.1948052 IF=4.783 Q2
Krizsma Sz. G.,
Kovács N. K.,
Kovács J. G.,
Suplicz A.: In-situ monitoring of deformation in rapid prototyped injection molds. Additive Manufacturing,
42, 102001/1-102001/8 (2021)
10.1016/j.addma.2021.102001 IF=11.632 D1
Tábi T., Csézi G., Kovács N. K.: 3D nyomtatott biokompozit vázszerkezetű fröccsöntött termékek vizsgálata. Polimerek, 6, 1042-1046 (2020)
Fris D. R.,
Szabó F.: Modelling of segregation during injection moulding. IOP Conference Series: Materials Science and Engineering,
903, 012022/1-012022/8 (2020)
doi:10.1088/1757-899X/903/1/012022Semperger O. V., Suplicz A.: The effect of titanium dioxide on the moisture absorption of polyamide 6 prepared by T-RTM. in '12th Hungarian Conference on Materials Science Balatonkenese, Magyarország. 2019.10.13-2019.10.15,8 (2020)
Fris D. R., Szabó F.: Hálófinomítási eljárás fejlesztése fröccsöntési szimulációs alkalmazásokhoz. in 'XXVIII. Nemzetközi Gépészeti Konferencia – OGÉT 2020 Online, . 2020.04.25.-2020.04.26,57-60 (2020)
Suplicz A., Boros R., Semperger O. V.: Investigation of the interfacial adhesion of glass bead-filled multicomponent injection moulded composites. in '12th Hungarian Conference on Materials Science Balatonkenese, Magyarország. 2019.10.13-209.10.15,7 (2020)
Boros R., Tóth N. Gy., Kovács J. G.: Ráfröccsöntéssel készült alkatrészek vizsgálati módszerének fejlesztése. in 'XXVIII. Nemzetközi Gépészeti Konferencia – OGÉT 2020 online konferencia. 2020.04.25.,41-44 (2020)
Semperger O. V.,
Suplicz A.: The Effect of the Parameters of T-RTM on the Properties of Polyamide 6 Prepared by in Situ Polymerization. Materials,
13, 4-14 (2020)
10.3390/ma13010004 IF=3.623 Q1
Tóth Cs., Kovács N. K.: Additív gyártástechnológiával készült, politejsav mátrixú kompozitok vizsgálata. Polimerek, 6, 926-930 (2020)
Boros R.,
Sibikin I.,
Ageyeva T.,
Kovács J. G.: Development and Validation of a Test Mold for Thermoplastic Resin Transfer Molding of Reactive PA-6. Polymers,
12, 976/1-976/13 (2020)
doi:10.3390/polym12040976 IF=4.329 Q1
Tóth Cs., Kovács N. K.: Characterization of short fiber-reinforced polylactic acid composites produced with Fused Filament Fabrication (FFF). in '12th Hungarian Conference on Materials Science Balatonkenese, Magyarország. 2019.10.13-2019.10.15,8 (2020)
Suplicz A.,
Semperger O. V.,
Kovács J. G.: Modeling the Thermal Conductivity Inhomogeneities of Injection-Molded Particle-Filled Composites, Caused by Segregation. Polymers,
11, 1691/1-1691/12 (2019)
10.3390/polym11101691 IF=3.426 Q1
Semperger O. V., Suplicz A.: Titán-dioxid hatása az in-situ polimerizációval előállított poliamid 6 minták tulajdonságaira. Polimerek, 5, 730-733 (2019)
Ageyeva T.,
Horváth Sz.,
Kovács J. G.: In-Mold Sensors for Injection Molding: On the Way to Industry 4.0. Sensors,
19, 3551/1-3551/21 (2019)
10.3390/s19163551 IF=3.275 Q1
Ageyeva T.,
Sibikin I.,
Kovács J. G.: A Review of Thermoplastic Resin Transfer Molding: Process Modeling and Simulation. Polymers,
11, 1555/1-1555/28 (2019)
10.3390/polym11101555 IF=3.426 Q1
© 2014 BME Department of Polymer Engineering - Created by: Dr. Romhány Gábor