Development of PEM fuel-cell stacks for utilization of hydrogen from renewable sources
Project ID:
2017-2.3.7-TÉT-IN-2017-00049
Supported by:
Hungarian National Research, Development and Innovation Office (NKFIH)
Term:
1 July 2018 - 30 June 2021
Supervisor (BME):
Dr. József Gábor Kovács
Dr. András Suplicz
Participant researchers (BME):
Dr. József Gábor Kovács
Dr. András Suplicz
Consortium partners (BME):
Indian Institute of Technology – Madras
Magyar Tudományos Akadémia, Természettudományi Kutatóközpont
Flaar Kft.
Project summary
One of the most promising energy carriers of the future is hydrogen, which is environmentally friendly because it produces water by reacting with oxygen to produce energy. The most efficient way to convert the chemical energy stored in hydrogen the use of fuel cells. Catalytic electrodes, which generally consist of activated carbon and platinum, are the most important components of low-temperature fuel cells. The porous structure of the activated carbon (carrier) ensures that the catalytic platinum - applied to its surface – and the fuel come into contact on the largest surface. The carrier must also be an electrical conductor to pass through the electrons generated in the catalyst reaction. An important requirement for the catalyst is the long service life. In applications with high demands, such as vehicles where frequently varying power demands, accelerations-decelerations, stoppages-start-ups destroy their structure, the stability of the activated carbon-platinum combination is unsatisfactory. Our research aims to develop a new, more resistant catalyst. We plan to combine the carbon carrier with titanium dioxide, which has a stronger interaction with platinum and is modified with other metals (molybdenum, tungsten, niobium) to provide proper electrical conductivity. Another important component of fuel cells is the bipolar plate, which provides the connection of the components of the device. Instead of the conventional less acid-resistant metal bipolar plates, we design new plastic based bipolar plates. The purpose of the new process is to achieve higher filler contents and thus better conductivity compared to conventional injection molded ones. We expect that from the new type of components a more stable and cheaper fuel cell can be built.
Project results
Section 1
1 July 2018 - 30 June 2019
In the project's first step, we prepared monocomposites with 0-40 m% filler content using polypropylene, graphite and carbon black. The samples were subjected to mechanical, thermal, morphological and conductivity measurements. Based on the mechanical tests, it was shown that increasing the graphite content and the carbon black content significantly reduced the elongation associated with the failure. From the electrical conductivity test, we have shown that a minimum of 30 m% of graphite is required to exceed the percolation limit. When carbon black was used, the conductivity did not improve significantly, so the percolation limit for this filler can be set above 30 m%. Subsequently, hybrid composites using graphite and carbon black were developed. Compared to monocomposites, the electrical conductivity was significantly improved so that the two fillers can work well together in a hybrid system. Using a special injection molding tool for mono- and bipolar plates, we fabricated bipolar plates from the developed hybrid filler system composite. The conductivity of the injection-molded hybrid filler system bipolar plates was found to be 5.9 S/cm.
A three-dimensional model of a prototype bipolar plate was prepared for simulation analysis. Injection molding simulations were performed to map the pattern. For the simulations, different material models were developed to analyze the effect of the filler volume, and hence the viscosity increase, on the injection pressure demand.
In addition, we analyzed the process of filler distribution along the flow path during mold cavity filling, which can have a significant impact on product properties such as shrinkage or local electrical and thermal conductivity. Mathematical models have been developed to describe the process and the measurement results on the analog models and have been used to develop and validate the simulation methods.
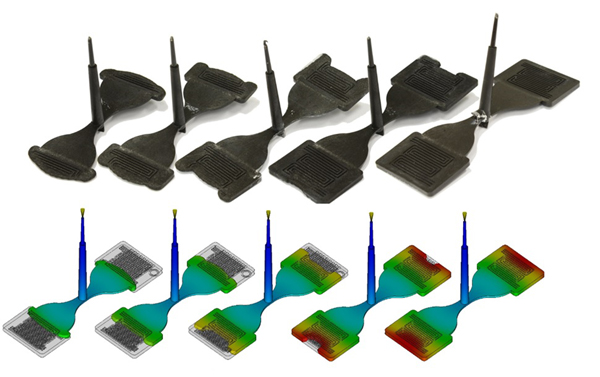
Section 2
1 July 2019 - 30 June 2020
In this milestone, an extensive literature research was conducted on the preparation of polyamide 6 by anionic ring-opening polymerization. Using the knowledge gained from this research, polyamide 6 samples were successfully prepared from caprolactam using C10 and C20P (catalyst and activator, respectively) by in-situ polymerization using a special casting apparatus. The samples were subjected to comprehensive tests (thermal, mechanical, morphological, etc.), and it was shown that the residual monomer content significantly influences their properties. Subsequently, filled samples were prepared with a dylactamate catalyst, as the conversion efficiency was very low using C10 due to the moisture content of graphite. Three different dosing methods were developed for the filled samples. When measuring the conductivity, it was found that the percolation limit was exceeded when 10 vol% graphite powder was used, resulting in a specific conductivity of 0.28 S/cm. Compared to the result presented in the previous milestone, 10 vol% less filler concentration is needed for samples prepared with in situ process to be conductive that in the case of melt processing, presumably due to good surface contact and proper impregnation. Thus, even higher conductivity can be achieved using the same amount of filler compared to conventional methods. In addition, several geometries for bipolar plate design were prepared and a CAD model of a universal mold was designed.
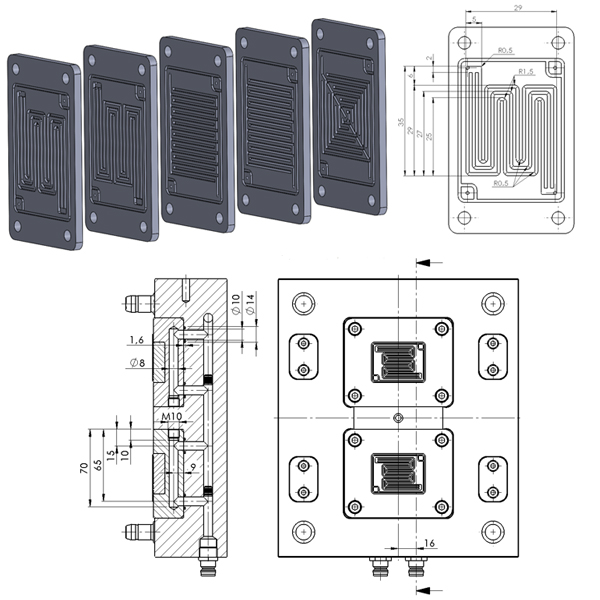
Section 3
1 July 2020 - 30 June 2021
In our research, we mainly investigated the polymerization processes of caprolactam. Increasing the catalyst content in the system and drying the fillers properly helped to achieve a high conversion efficiency, and thus a filler content of up to 40 m% was achieved. For the graphite-filled composites prepared in this way, we were able to reduce the filler content required to achieve percolation by more than 10 m% compared to conventional injection molding technology (7 m% for expanded graphite and 37 m% for natural graphite). The highest conductivities were obtained for 20 m% expanded graphite and 50 m% natural graphite, with values of 0.21 and 0.08 S/cm, respectively. The carbon-based fillers used only slightly decreased the hardness of the samples, increased their stiffness, reduced their tensile strength and elongation at break. For the conventional method of melt mixing, we were able to perform tests at 0-70 m% filler content. Conductivity measurements showed that carbon black and expanded graphite gave the lowest percolation threshold (16.3 and 17.5 m%, respectively) and the highest conductivity (2.7 S/cm (50 m%); 19.9 S/cm (70 m%), respectively). A hybrid effect was observed between the two fillers, which positively influences the conductivity. Finally, the results obtained were used to prepare composite bipolar plates with a conductivity of 21 S/cm.
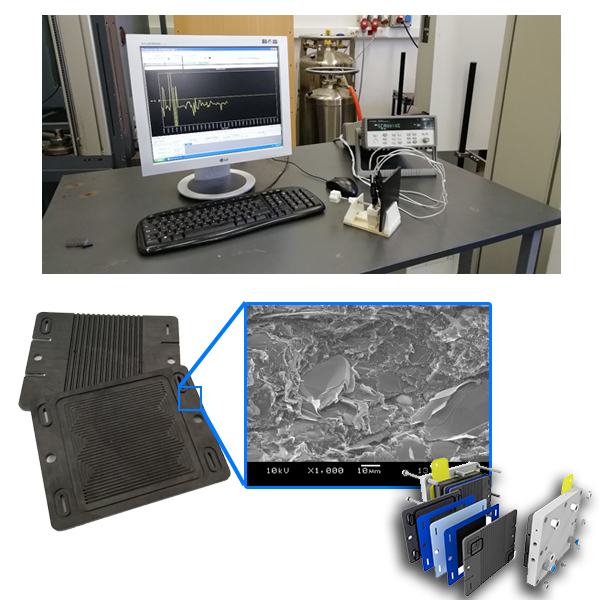
Project-related publications
Semperger O. V.,
Suplicz A.: The effect of the titanium dioxide nanoparticles on the morphology and degradation of polyamide 6 prepared by anionic ring-opening polymerization. Polymer Engineering and Science,
62, 2079-2088 (2022)
10.1002/pen.25990 IF=3.2 Q2
Zink B.,
Kovács J. G.: Pressure‐dependent heat transfer coefficient measurement for thermoplastic melts. Polymer Engineering and Science,
62, 1137-1146 (2022)
10.1002/pen.25912 IF=3.2 Q2
Ageyeva T.,
Kovács J. G.,
Tábi T.: Comparison of the efficiency of the most effective heterogeneous nucleating agents for Poly(lactic acid). Journal of Thermal Analysis and Calorimetry,
147, 8199-8211 (2022)
10.1007/s10973-021-11145-y IF=4.4 Q1
Török D.,
Ageyeva T.,
Boros R., Kovács Á.,
Kovács J. G.: Developing a method for evaluating color changeover in a hot-runner multi-cavity injection mold. Polymer Testing,
115, 107759/1-107759/9 (2022)
10.1016/j.polymertesting.2022.107759 IF=5.1 D1
Boros R.,
Ageyeva T., Golcs Á., Krafcsik O. H.,
Kovács J. G.: Plasma treatment to improve the adhesion between ABS and PA6 in hybrid structures produced by injection overmolding. Polymer Testing,
106, 107446/1-107446/11 (2022)
10.1016/j.polymertesting.2021.107446 IF=5.1 D1
Török D.,
Zink B.,
Ageyeva T., Hatos I., Zobač M., Fekete I.,
Boros R., Hargitai H.,
Kovács J. G.: Laser powder bed fusion and casting for an advanced hybrid prototype mold. Journal of Manufacturing Processes,
81, 748-758 (2022)
10.1016/j.jmapro.2022.07.034 IF=6.2 Q2
Tábi T.,
Pölöskei K.: The effect of processing parameters and Calcium-stearate on the ejection process of injection molded Poly(Lactic Acid) products. Periodica Polytechnica-Mechanical Engineering,
66, 17-25 (2022)
10.3311/PPme.18246 IF=1.3
Rajamani P. K.,
Ageyeva T.,
Kovács J. G.: Personalized mass production by hybridization of additive manufacturing and injection molding. Polymers,
13, 309/1-309/19 (2021)
10.3390/polym13020309 IF=4.967 Q1
Semperger O. V., Pomlényi P., Suplicz A.: Felület-bevonatolási eljárás T-RTM technológiához. Polimerek, 7, 186-192 (2021)
Krizsma Sz. G.,
Kovács N. K.,
Kovács J. G.,
Suplicz A.: In-situ monitoring of deformation in rapid prototyped injection molds. Additive Manufacturing,
42, 102001/1-102001/8 (2021)
10.1016/j.addma.2021.102001 IF=11.632 D1
Szuchács A.,
Ageyeva T.,
Boros R.,
Kovács J. G.: Bonding strength calculation in multicomponent plastic processing technologies. Materials And Manufacturing Processes,
36, 151-159 (2021)
10.1080/10426914.2021.1948052 IF=4.783 Q2
Szabó F.,
Suplicz A.,
Kovács J. G.: Development of injection molding simulation algorithms that take into account segregation. Powder Technology,
389, 368-375 (2021)
10.1016/j.powtec.2021.05.053 IF=5.64 Q1
Krizsma Sz. G., Suplicz A.: Additív gyártástechnológiával előállított fröccsöntő szerszámbetétek üzem közbeni deformációinak vizsgálata. Polimerek, 7, 155-160 (2021)
Tábi T.,
Ageyeva T.,
Kovács J. G.: Improving the ductility and heat deflection temperature of injection molded Poly(lactic acid) products: A comprehensive review. Polymer Testing,
101, 107282/1-107282/36 (2021)
10.1016/j.polymertesting.2021.107282 IF=4.931 D1
Boros R.,
Sibikin I.,
Ageyeva T.,
Kovács J. G.: Development and Validation of a Test Mold for Thermoplastic Resin Transfer Molding of Reactive PA-6. Polymers,
12, 976/1-976/13 (2020)
doi:10.3390/polym12040976 IF=4.329 Q1
Semperger O. V., Suplicz A.: The effect of titanium dioxide on the moisture absorption of polyamide 6 prepared by T-RTM. in '12th Hungarian Conference on Materials Science Balatonkenese, Magyarország. 2019.10.13-2019.10.15,8 (2020)
Suplicz A., Boros R., Semperger O. V.: Investigation of the interfacial adhesion of glass bead-filled multicomponent injection moulded composites. in '12th Hungarian Conference on Materials Science Balatonkenese, Magyarország. 2019.10.13-209.10.15,7 (2020)
Fris D. R.,
Szabó F.: Modelling of segregation during injection moulding. IOP Conference Series: Materials Science and Engineering,
903, 012022/1-012022/8 (2020)
doi:10.1088/1757-899X/903/1/012022Semperger O. V.,
Suplicz A.: The Effect of the Parameters of T-RTM on the Properties of Polyamide 6 Prepared by in Situ Polymerization. Materials,
13, 4-14 (2020)
10.3390/ma13010004 IF=3.623 Q1
Fris D. R., Szabó F.: Hálófinomítási eljárás fejlesztése fröccsöntési szimulációs alkalmazásokhoz. in 'XXVIII. Nemzetközi Gépészeti Konferencia – OGÉT 2020 Online, . 2020.04.25.-2020.04.26,57-60 (2020)
Suplicz A.,
Semperger O. V.,
Kovács J. G.: Modeling the Thermal Conductivity Inhomogeneities of Injection-Molded Particle-Filled Composites, Caused by Segregation. Polymers,
11, 1691/1-1691/12 (2019)
10.3390/polym11101691 IF=3.426 Q1
Semperger O. V., Suplicz A.: Titán-dioxid hatása az in-situ polimerizációval előállított poliamid 6 minták tulajdonságaira. Polimerek, 5, 730-733 (2019)
Semperger O. V., Suplicz A.: Titán-dioxid hatása az in-situ polimerizációval előállított poliamid 6 minták tulajdonságaira. in 'XXVII. Nemzetközi Gépészeti Konferencia OGÉT 2019 Nagyvárad, Románia. 2019.04.25.-2019.04.28,472-475. (2019)
Zink B.,
Kovács N. K.,
Kovács J. G.: Thermal analysis based method development for novel rapid tooling applications. International Communications in Heat and Mass Transfer,
108, 104297/1-104297/9 (2019)
10.1016/j.icheatmasstransfer.2019.104297 IF=3.971 Q1
Ageyeva T.,
Sibikin I.,
Kovács J. G.: A Review of Thermoplastic Resin Transfer Molding: Process Modeling and Simulation. Polymers,
11, 1555/1-1555/28 (2019)
10.3390/polym11101555 IF=3.426 Q1
© 2014 BME Department of Polymer Engineering - Created by: Dr. Romhány Gábor