Development of high performance damage tolerant and damage indicating hybrid composites
Project ID:
PD 121121
Supported by:
Hungarian National Research, Development and Innovation Office (NKFIH)
Term:
1 October 2016 - 30 September 2019
Supervisor (BME):
Dr. Gergely Czél
Project summary
One of the biggest challenges for the 21st century’s transportation sector in line with the strategic aims of the EU is to improve fuel economy and reduce emissions, which may be done by reduction of the gross weight of vehicles. The development of the next generation of economic and environmentally friendly vehicles requires high strength and low weight components. So-called composite materials consisting of fibres and plastic resins offer high strength but usually fail in a catastrophic way without sufficient warning. This unsafe failure character renders them unsuitable for several applications where loads are unpredictable and sudden failure cannot be tolerated. This research programme aims at developing a new generation of composites featuring safe, gradual failure, with significant margin between a detectable warning and final failure. Our approach is to mix (hybridise) fibre types and design the layered architecture of our new materials to mimic the safe failure of metals. Our previous success in developing hybrid composites showing damage tolerance in one direction encourages us to develop more advanced types which can be loaded in any directions. Our new materials could potentially offer a notable increase in the scope of composite applications including transportation and construction sectors. A significant shift in the conservative design limits leading to lower component weights and therefore operational cost savings could potentially take place as well due to safer failure character of the new damage tolerant composites.
Project results
Section 1
1 October 2016 - 30 September 2017
Previously, around 3 mm thick unidirectional asymmetric glass/carbon-epoxy hybrid specimens were designed and the compressive damage and failure mechanisms of three layer glass/thin carbon hybrid blocks were investigated in four point bending test setup. This new test setup was developed to allow for damage and failure type observations, which are extremely challenging in case of the conventional direct compression test setup where the specimens typically fail catastrophically. The strains were monitored by a novel optical measurement procedure based on the tracked positions of five markers on the edge of the bending specimens and the radii of circular arcs fitted onto the marker positions. A new failure mechanism was observed which has not been reported in the international scientific literature yet: The high and ultra-high modulus carbon layers have shown stable, distributed fragmentation. This type of failure has only been shown under tensile loading so far and suggests that it may be possible to exploit the fragmentation as a key ductility mechanism in compression as well as tension dominated load scenarios and in the variety of corresponding applications.
The compressive behaviour of glass/carbon hybrid materials was analysed further and experimental work was executed to understand the damage development and mechanisms in the carbon layer and at the glass/carbon layer interface. Four point bending specimens with carbon layers close to their top surface were deformed in a purpose-designed steel frame. The frame was put under optical and scanning electron microscope to analyse the damage modes and the micro-deformations in the hybrid material under compressive deformation. Fragmentation of the thin ultra high modulus carbon layer in the hybrid specimens in compression was confirmed. Sliding of the fragments along the inclined fracture surfaces and local delaminations at the crack tips were also revealed by close-up micrographs.
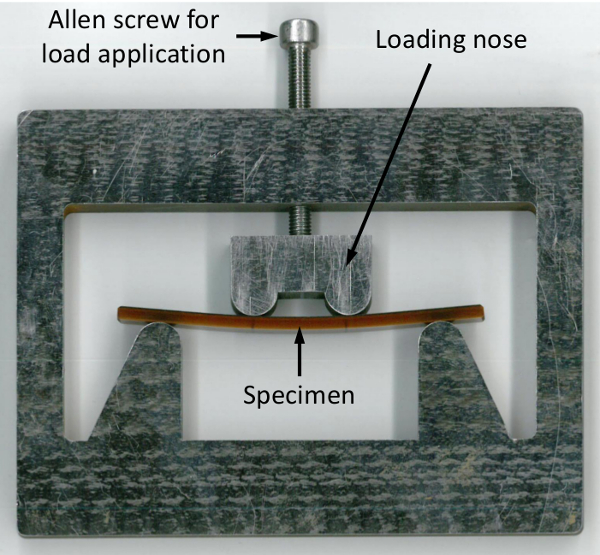
Four point bending specimen loaded in a steel frame designed to be suitable for microscopy
Section 2
1 October 2017 - 30 September 2018
The tensile response of unidirectional carbon/carbon hybrid specimen types comprising ultra-high modulus (UHM), high modulus (HM), and intermediate modulus (IM) carbon/epoxy layers were investigated in preparation for the more complicated multi-directional carbon/carbon hybrid laminate design. Favourable pseudo-ductile failure behaviour with linear-plateau-linear style stress-strain responses was demonstrated with progressive damage accumulation due to low strain material fragmentation and stable delamination instead of sudden, catastrophic fracture typical of conventional unidirectional composites. All five material combinations exhibited exceptionally high initial moduli and a wide stress plateau with further increase in stress both of which can be exploited as a warning of accumulating damage before final failure.
Multi-directional interlayer hybrid composites of ultra-high modulus (UHM) and intermediate modulus (IM) carbon/epoxy were designed and characterised both under un-notched and notched conditions. The motivation for this key task was to trigger a break-through in the exploitation of the ductility mechanisms demonstrated in our unidirectional hybrid composites, as multi-directional pseudo-ductile laminates can be suitable for a wide range of applications not being limited to uniaxial load scenarios. The selection of constituent materials was based on the results of the previous studies of unidirectional configurations. Both tested un-notched configurations with different constituents (3 layer hybrid sublaminates) and the same lay-up sequence: [45/90/-45/0]s exhibited favourable linear-plateau style pseudo-ductile failure mode due to fragmentation of the low strain material in the 0° hybrid sublaminate. Reduced notch sensitivity similar to the ductile net-section behaviour of metals was achieved in both hybrid laminates due to local damage and induced load re-distribution around the notches, for both open holes and sharp notches.
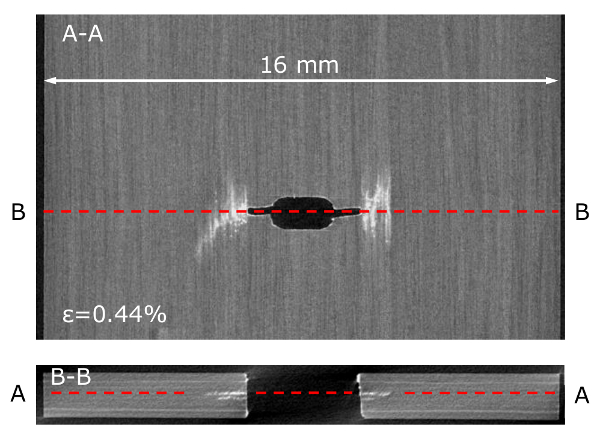
X-ray computed tomography image showing local damage next to the notch in a pseudo-ductile multidirectional hybrid laminate
Section 3
1 October 2018 - 30 September 2019
An experimental campaign was completed to assess the visual strain overload indicating capability of carbon/glass hybrid composites due to the translucent glass layer which can reveal carbon layer fractures and interfacial damage. The results demonstrated that it is possible to use a retrofitted thin sensor patch of about 10x50 mm to indicate if a component (eg. a flat carbon/epoxy composite rod) was deformed beyond a pre-defined strain in tension. The key design parameters and the most important factors affecting the accuracy of the sensors were identified. The technology was demonstrated on a bike handlebar. The previously demonstrated hybrid composite visual overload sensor was also applied at a larger scale not only as a retrofitted patch on tensile test specimens but as a multifunctional structural sensing layer on a 600x300 mm pseudo-ductile sandwich panel as well as on a full-scale longboard (up to 1 m long). These components are large enough to represent small-scale feasibility studies with realistic load scenarios. The structural sensing layer of the sandwich panel successfully gave warning of bending overload (see figure) at the beginning of a benign, progressive damage accumulation process well before the final failure of the sandwich beam specimens. The feasibility studies demonstrated that the developed materials and overload sensing technology can be applied to safety-critical components of medium size.
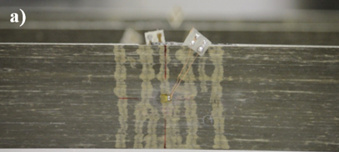
Multi-functional structural and sensing layer after overload
Project-related publications
Marino S. G.,
Czél G.: Improving the performance of pseudo-ductile hybrid composites by film-interleaving. Composites Part A: Applied Science and Manufacturing,
142, 106233/1-106233/16 (2021)
10.1016/j.compositesa.2020.106233 IF=9.463 Q1
Marino S. G.,
Czél G.: Improving the performance of pseudo-ductile hybrid composites by film-interleaving. Composites Part A: Applied Science and Manufacturing,
142, 106233/1-106233/16 (2021)
10.1016/j.compositesa.2020.106233 IF=9.463 Q1
Wisnom M., Potter K., Czél G., Jalalvand M.: Strain overload sensor. GB2544792B, United Kingdom (2020)
Marino S.G., Mayer F., Bismarck A.,
Czél G.: Effect of plasma-treatment of interleaved thermoplastic films on delamination in interlayer fibre hybrid composite laminates. Polymers,
12, 2834/1-2834/24 (2020)
10.3390/polym12122834 IF=4.329 Q1
Csallány E. K., Czél G.: Rendezett nem folytonos szálakkal erősített, nagy teljesítményű polimer kompozitok mechanikai tulajdonságai nyomó terhelés esetén. Polimerek, 5, 388-392 (2019)
Suwarta P., Fotouhi M.,
Czel G., Longana M., Wisnom M. R.: Fatigue behaviour of pseudo-ductile unidirectional thin-ply carbon/epoxy-glass/epoxy hybrid composites. Composite Structures,
224, UNSP 11099/1-UNSP 11099/ (2019)
10.1016/j.compstruct.2019.110996 IF=5.138 D1
Rev T., Jalalvand M., Fuller J., Wisnom M. R.,
Czél G.: A simple and robust approach for visual overload indication - UD thin-ply hybrid composite sensors . Composites Part A: Applied Science and Manufacturing,
121, 376-385 (2019)
10.1016/j.compositesa.2019.03.005 IF=6.444 D1
Wisnom M. R., Czél G., Fotouhi M., Fuller J., Jalalvand M., Rev T., Wu X.: Reduced tensile notch-sensitivity in pseudo-ductile thin-ply composites. in '18th European Conference on Composite materials, ECCM18 Athens, Greece. 2018.06.24-2018.06.28.,1-7 (2018)
Rév T., Czél G., Wisnom M. R.: A Novel Test Method to Induce Bi-axial Stress States in Thin-ply Carbon Composites Under Combined Longitudinal Tension and Transverse Compression. in 'American Society for Composites—Thirty-Third Technical Conference on Composite Materials Seattle, USA. 2018.09.24. - 2018.09.,9 (2018)
Czél G., Bugár-Mészáros M., Wisnom M. R.: The effect of test temperature on the pseudo-ductility of thin-ply hybrid composites. in '18th European Conference on Composite materials, ECCM18 Athens, Greece. 2018.06.24-2018.06.28.,1-8 (2018)
Suwarta P., Czél G., Fotouhi M., Rycerz J., Wisnom M. R.: Pseudo-ductility of Unidirectional Thin Ply Hybrid Composites in Longitudinal Compression. in 'American Society for Composites—Thirty-Third Technical Conference on Composite Materials Seattle, USA. 2018.09.24. - 2018.09.,10 (2018)
Czél G., Rev T., Jalalvand M., Fotouhi M., Longana M. L., Nixon-Pearson O. J., Wisnom M. R.: Pseudo-ductility and reduced notch sensitivity in multi-directional all-carbon/epoxy thin-ply hybrid composites. Composites Part A: Applied Science and Manufacturing,
104, 151-164 (2018)
10.1016/j.compositesa.2017.10.028 IF=6.282 D1
Czél G., Jalalvand M., Wisnom M. R.,
Czigány T.: Design and characterisation of high performance, pseudo-ductile all-carbon/epoxy unidirectional hybrid composites. Composites Part B: Engineering,
111, 348-356 (2017)
10.1016/j.compositesb.2016.11.049 IF=4.92 D1
© 2014 BME Department of Polymer Engineering - Created by: Dr. Romhány Gábor