Microstructure design and properties of graphene/rubber nanocomposites for high performance tires
Project ID:
2017-2.3.6-TÉT-CN-2018-00002
Supported by:
Hungarian National Research, Development and Innovation Office (NKFIH)
Term:
1 July 2019 - 30 June 2022
Supervisor (BME):
Dr. Tamás Bárány
Dr. Péter Tamás-Bényei
Participant researchers (BME):
Dr. Tamás Bárány
Dr. István Zoltán Halász-Kutasi
Dávid Zoltán Pirityi
Dániel Ábel Simon
Viktor Hliva
Balázs Magyar
Dr. László Mészáros
Dr. Roland Petrény
Dr. Márton Tomin
Dr. Ábris Dávid Virág
Consortium partners (BME):
Beijing University of Chemical Technology
Project summary
Nowadays low rolling resistance tyres with high wear resistance attract more and more attention, as they decrease fuel consumption on the one hand and increase tyre mileage on the other. Another important factor is that these tyres can also decrease the amount of dust in cities, as one source of dust is microparticles generated by the wear of tyres. For this reason, research into environmentally friendly, “green” tyres is a strategically important area in many countries. The aim of this research is to develop rubber mixtures that can be used in the manufacturing of such low rolling resistance and high wear resistance tyres with the use of novel nano-reinforcements and manufacturing technologies. The knowledge acquired with the research will greatly help the targeted design of rubber products (not only tyres) instead of the present trial and error method.
Project results
Section 1
1 July 2019 - 30 June 2020
We conducted a thorough literature overview about the most relevant topics concerning the project. We included the preparation technologies, mechanical properties and industrial applications of graphene and graphene oxide reinforced, elastomer-based nanocomposites.
We found that it is impossible to source reliable, good quality graphene from the market, so we decided to produce it ourselves. Based on our literature review, we selected the improved Hummers’ method as our process route, during which graphite is turned into graphene oxide with the use of various oxidising agents. We faced some challenges during production, as it took us weeks of hard work to produce a single gram of graphene oxide. We soon figured that the bottleneck of the process was the small volume of our old centrifuge, so we purchased a new Sorvall X4 Pro type centrifuge with a capacity that is 5 times that of our old one. Also, we achieved relatively high yield: 3.5 g of graphene oxide can be produced from 5 g of graphite in the form of a 1 wt% aqueous suspension.
We also performed some preliminary experiments with regards the preparation and mechanical testing of graphene-reinforced styrene butadiene rubber. Our results showed that silica, carbon black and graphene cannot form a hybrid reinforcement structure without additional coupling agents. However, the combined use of carbon black and graphene showed some potential: 10 phr of graphene increased the elongation at break value of the rubber from 240% to 420% without changing the modulus of the sample, indicating good nanoreinforcement.
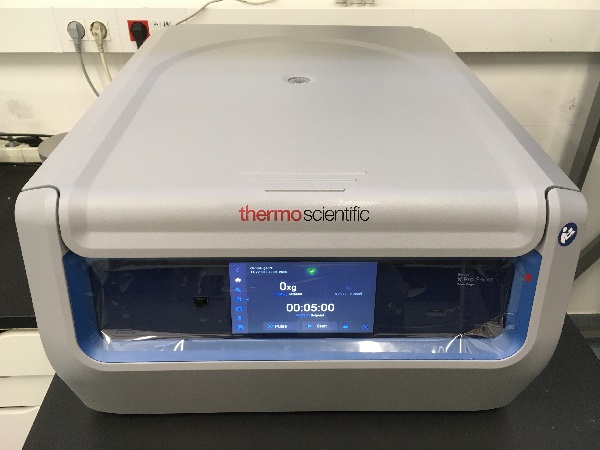
The new centrifuge after installation
Section 2
1 July 2020 - 30 June 2021
We compared the material testing methods we used with the ones available in scientific literature (along with the results achieved). In conclusion, we broadened our scope of testing methods so that we can measure the number of layers in graphene as well as its degree of oxidisation.
We holistically optimised rubber-based nanocomposites that were reinforced with silica, carbon black and graphene. Based on our results, we found that silane coupling agents can help the hybrid behaviour of the three nanomaterials. Hence, we are now prepared for the final section of the project whereby we will use graphene oxide in real, industrial rubber compounds. (So far, we have been using simplified rubber compositions.)
We set up the process of latex mixing in our lab. Based on our experiments, it is obvious that graphene oxide can be readily dispersed in rubber latex, and the resulting mixtures had superior dispersion compared to samples prepared via conventional methods. Also, we found that the inherent properties of the rubber latex have a very strong influence on the properties of the resulting rubber composites. This experimental set directly precedes our final goal of preparing masterbatches with high graphene oxide content.
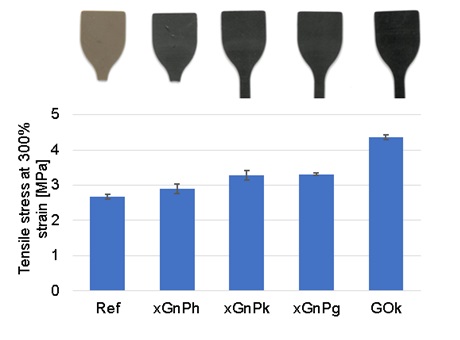
The darkness of graphene-reinforced, latex-mixed rubber samples vs. their tensile stress at 300% strain (Ref – unfilled, xGnPh – mixed on a two-roll mill, xGnPk – manual latex mixing, xGnPg – ultrason
Section 3
1 July 2021 - 30 June 2022
Based on the results from the previous 2 sections, we continued the development of graphene/elastomer nanocomposites. We determined the technological maximum concentration of silane coupling agent (6 phr), and also showed that silane has a more significant impact on the properties of vulcanisates than polyethylene-glicol. We have expanded our experiments to other rubber types too, and showed that in order to have comparable mixing techniques, the inherent Mooney viscosity of the base rubbers should be similar. We have also showed that the latex mixing of powdered fillers (carbon black, graphite, graphene or GO) has no benefit over melt mixing. In comparison, 1 phr of GO, rGO or in-situ rGO can increase the tensile strength of rubber by 60-80%.
Out of the mixing techniques we examined, latex mixing can maximise the reinforcing effects of GO and its derivatives. Melt mixing has considerably weaker effects. As an intermediate solution, we prepared masterbatches with 10 phr of GO derivatives via latex mixing. And these masterbatches were mixed with unfilled rubber via conventional melt mixing. Masterbatch mixing, despite being a significantly less complex technique, brought almost identical (slightly worse) results than latex mixing. While rGO and in-situ rGO contributed to higher tensile strength values than GO, these additives would increase the loss factor of the resulting rubber. Ultimately, our latex-mixed GO masterbatches were used to manufacture car tyre prototypes that had outstanding rolling resistance, contributing to improved fuel efficiency.

Selected properties of latex mixed nanocomposites with 1 phr of GO derivatives
Project-related publications
Sayfo P.,
Pirityi D. Z.,
Pölöskei K.: Characterization of graphene-rubber nanocomposites: a review. Materials Today Chemistry,
29, 101397/1-101397/17 (2023)
10.1016/j.mtchem.2023.101397 IF=6.7 Q1
Pirityi D. Z.,
Bárány T.,
Pölöskei K.: Hybrid reinforcement of styrene-butadiene rubber nanocomposites with carbon black, silica, and graphene. Journal of Applied Polymer Science,
139, e52766/1-e52766/13 (2022)
10.1002/app.52766 IF=3 Q2
Pirityi D. Z.,
Pölöskei K.: Development of graphite- and graphene reinforced styrene-butadiene rubber. Acta Materialia Transylvanica,
4, 103-108 (2021)
10.33924/amt-2021-02-09 Pirityi D. Z.,
Pölöskei K.: Grafit- és grafénerősítésű sztirol-butadién kaucsuk fejlesztése. Acta Materialia Transylvanica,
4, 103-108 (2021)
10.33923/amt-2021-02-09 Guo H., Ji P.,
Halász I. Z.,
Pirityi D. Z.,
Bárány T., Xu Z., Zheng L., Zhang L., Liu L., Wen S.: Enhanced fatigue and durability properties of natural rubber composites reinforced with carbon nanotubes and graphene oxide. Materials,
13, 5746/1-5746/12 (2020)
10.3390/ma13245746 IF=3.623 Q1
© 2014 BME Department of Polymer Engineering - Created by: Dr. Romhány Gábor