New concept for upgrading recycling of multicomponent packaging wastes and formation of product of high market value
Project ID:
2018-1.3.1-VKE-2018-00017
Supported by:
Hungarian National Research, Development and Innovation Office (NKFIH)
Term:
1 Marc 2019 - 31 August 2022
Supervisor (BME):
Dr. Kornél Pölöskei
Participant researchers (BME):
Dr. Tamás Bárány
Dr. Ákos Kmetty
Dr. Kornél Pölöskei
Dr. Tamás Tábi
Dr. Dániel Gere
Katalin Bordácsné Dr. Bocz
Dániel Vadas
Dr. Brigitta Bodzay
Dr. Beáta Szolnoki
Consortium partners (BME):
Pro-Form Kft. (konzorciumvezető)
Project summary
The project focuses on the polyolefins (PE,PP), which are the most widely used polymers in the packaging industry market. Most of the one-way PE packaging materials and thermoformed PET blisters, trays, boxes are deposited without any selection. Furthermore the industrial waste of multilayer thermoformed PET represent considerable secondary PET source. The use of this kind of secondary materials is hindered by application- and processing-technology barriers, thus great need exists for technology development leading to economic value preservation on one side and effective value increase on the other. The main aim of the research is to find new field of application for secondary PET wastes of lower value. These can be used for logistic trays (used by almost all industries) if special combination of properties can be set. These are currently produced from more expensive materials due to brittleness of PET. Products of good quality will be achieved in single production step by applying compounding units of optimized combination setting optimized parameters of production and wide-slit tool of best specification. Thus the granulation production phase can be waved and the thermoformed elements can be produced directly when the special twin screw extruder is applied. As a result the degradation, lowering the product quality, can be suppressed. The product, called recycled PET direct blend (RPET-DB), will be commercialized in the forms of flame retarded sheets/films/3D objects depending on the market demand. The expected success of the product can act as a model for the innovation of the utilization of other wastes. The aims will be realized along the run of the project by utilizing the methods of applied materials science and materials technology including application of multifunctional materials and considering cost efficiency. Metal ions of the metal-coated PET, acting as multifunctional component, will play a role in both the compatibilization and flame retardancy, furthermore, phosphoric acid esters ensure not only efficient flame retardancy but also make the product antistatic.
Project results
Section 1
1 Marc 2019 - 29 February 2020
We carried out a literature review of the raw materials related to the call for proposals, their recycling, and the processing technologies, as well as the methods suitable for their examination, which greatly helped the process of selecting the raw materials and the experiments performed. We conducted exploratory market research to identify those market segments and participants to whom we can provide marketable packaging products based on their preliminary expectations as a result of the development. Laboratory equipment suitable for testing secondary raw materials and films made from them, as well as a twin-screw flat film coextruder line suitable for extruding film from raw materials, and a radiant heated air-forming machine capable of producing samples and prototypes formed from films have been procured. Reference extrusion and molding experiments were performed.
The basic and auxiliary materials were procured and their physical and chemical characterization was performed. We performed a complex analysis of PET and PE waste from several sources, as well as an additive (flame retardant). We have prepared state-of-the-art literature summaries on the production, properties, recycling, and antistatic, hardening, compatibilization, and flame retardancy capabilities of PET.
Test samples were prepared by injection molding and sheet extrusion to modify the properties of recycled PET and PET / PE associated systems to meet special needs. Primarily for cost-effectiveness reasons, we always sought to use minimal additives in the value-adding modifications. As a completely new approach, we also used waste fractions in a targeted way, as a reactive component, and with multifunctional additives (eg flame retardant and amplifier, colorant and antistatic agent) we achieved multi-layered property improvement.
With the help of the performed various material structure studies, we explored the interactions between the components and their property-modifying effect.
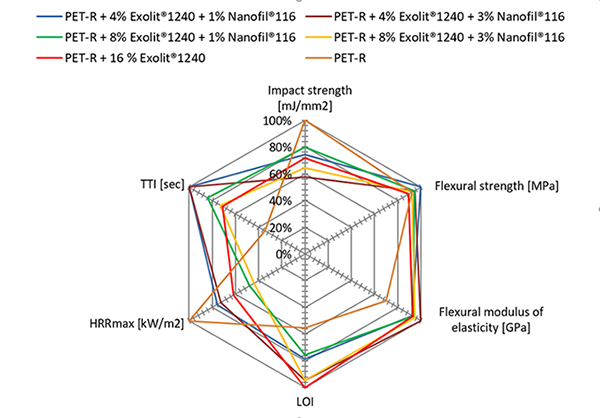
Comparative diagram of key physical parameters of V-0 rated recycled materials
Section 2
1 Marc 2020 - 28 February 2021
During the milestone, the most favorable value-adding additive combinations (compatibilizers, antistatic agents, flame retardants, impact strengths) were selected based on the requirements of the product groups explored by Pro-Form Ltd. We were the first to recognize that highly degraded rPET fractions are able to form a special short-chain boundary layer around the particles of a reactive additive dispersed in the polymer matrix, which can multiply the improvement in product properties. Utilizing the invention, we were able to achieve improvements in flame retardancy and mechanical properties at the same time; We achieved a 50% reduction in heat emissions with a 40% increase in impact strength using an exceptionally high recycled raw material of over 60%. The homogenization, increase of value (flame retardancy and increase of impact strength) of the multicomponent polymer waste and the production of the final product were realized in a single integrated production process. In the case of technology based on the use of a significant amount of secondary raw materials, we plan to guarantee constant product quality with a camera monitoring system installed on the production line, the sensitivity and applicability of which have already been successfully demonstrated in semi-operational conditions.
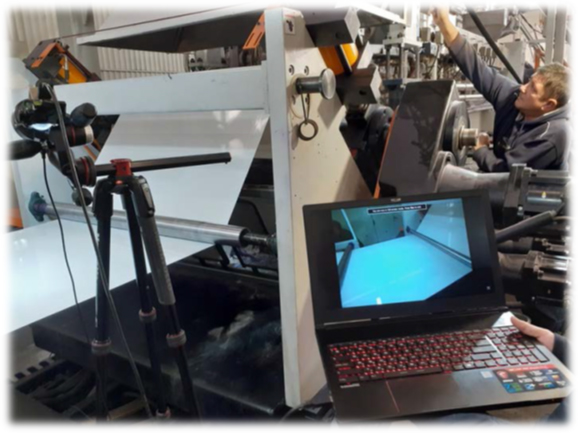
Quality control of products manufactured under industrial conditions developed during the project
Section 3
1 Marc 2021 - 28 February 2022
We have discovered that during compounding with controlled moisture content, a tough phase boundary layer composed of short molecular chains can be formed through enhanced hydrolytic degradation of PET. As a result, we achieved more than a 6-fold increase in grooved impact work by “adding some water” to the system or omitting the drying step. Taking advantage of this phenomenon, products with excellent impact strength (> 50 kJ / m2), toughness (elongation: 140%) and at the same time excellent strength (40 MPa) and stiffness (1500 MPa) can be produced with significantly lower (up to 50%) elastomer content and simplified technology. The possibility of omitting the drying step results in a further reduction in production costs. We found that the outstanding increase in impact work was due to the more intense reactive compatibility of PET / EBA-GMA and the inhibited crosslinking of the elastic phase. An international PCT patent application has been filed to protect the intellectual property of the invention (PCT / HU2021 / 050064).
We have produced sheet products for confectionery packaging based on a high recycled content (~ 60%) of compatible PET / PE blends, the impact resistance of which is characterized by a perforation energy value of about 10 times. We implemented camera monitoring of plate extrusion processes. In addition to the continuous, in-line instrumental tracking and registration of color changes, we also demonstrated the automatic detection of various manufacturing defects.
We have shown that by using a masterbatch of a carbon black-free, iron oxide-based dye, the heat release during the combustion of logistics trays can be reduced by a maximum of about 50%. Based on the complex recipes tested by BME, the perforation energy of the PET / PE-based logistics trays with at least 50% recycled and 50% reduced heat emissions manufactured by Pro-Form Kft is much higher than the 40% undertaken among the project objectives. It has increased 10 times - compared t
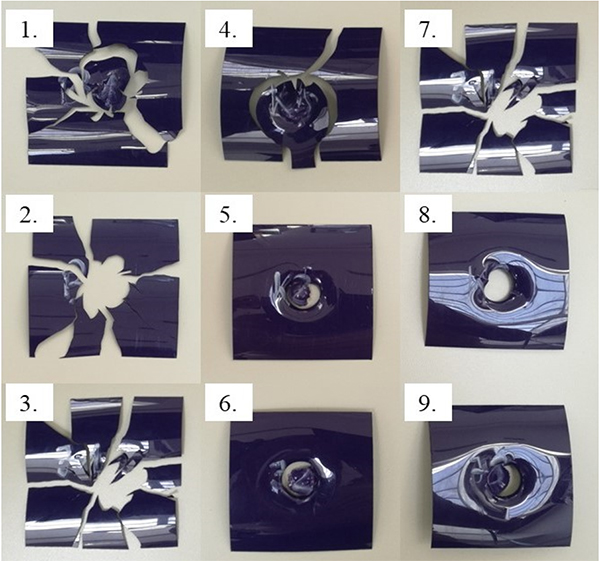
Drop test specimens of film containing 30 m% original and 70 m% recycled PET after the test, where both brittle, tough and intermediate failure can be observed
Section 4
1 Marc 2022 - 31 August 2022
After the evaluation of the previous semi-factory experiments, Pro-Form Ltd carried out the production film extrusion and thermoforming experiments with specific raw material compositions, and at the end of the work phase, the product portfolio intended for the market was created. Logistics trays with outstanding impact resistance and fire resistance can be used by industrial players who use such products for external or internal movements, and they can replace their currently used logistics trays, typically made of non-recycled materials, with a more economically favorable alternative. Furthermore, in the course of our research, we have developed raw material compositions that can also serve as the raw material for food industry packaging products, as the middle layer of the film contains a recycled PET/PE blend containing appropriate amounts of compatibilizing additives, and the cover layer made of the original material is in direct contact with the food. In addition to these, as a result of the development, we also produced blister packs that, thanks to their transparency, were typically made for the household and chemical industry.
Fine-tuning of the recipes and production technology of the plates used as the raw material for logistics trays with increased impact resistance and at the same time fire-resistant, manufactured under industrial conditions, to the product-specific requirements was realized. We built a camera monitoring system on the extrusion production line, which ensures continuous in-line instrumental monitoring of technologies based on the use of a high proportion of secondary raw materials. The prototypes produced by industry were extensively qualified by the BME with extensive mechanical, morphological, thermal, flammability and other application technical tests. Based on the results, with the cooperation of the two partners, the adaptive feedback of the product properties to the product requirements took place, and then the recipes and product
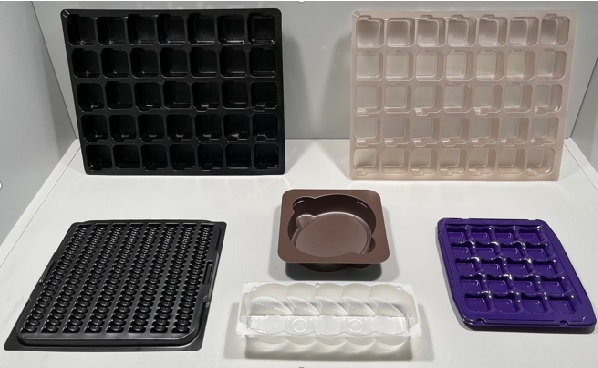
Products made from foils developed during the project
Project-related publications
Bocz K.,
Ronkay F. Gy., Vadas D.,
Molnár B.,
Gere D.,
Czigány T.,
Marosi Gy.: Flame retardancy of PET foams manufactured from bottle waste. Journal of Thermal Analysis and Calorimetry,
148, 217-228 (2023)
10.1007/s10973-022-11423-3 IF=3 Q2
Ronkay F. Gy.,
Molnár B., Szabó E.,
Marosi Gy. , Bocz K.: Water boosts reactive toughening of PET. Polymer Degradation and Stability,
203, 9 (2022)
10.1016/j.polymdegradstab.2022.110052 IF=5.9 D1
Decsov K. E., Ötvös B.,
Marosi Gy., Bocz K.: Microfibrous cyclodextrin boosts flame retardancy of poly(lactic acid) II - phosphorous silane treatment further enhances the effectivity. Polymer Degradation and Stability,
200, 109938/1-109938/11 (2022)
10.1016/j.polymdegradstab.2022.109938 IF=5.9 D1
Nguyen Thanh, T. T., Decsov K. E., Bocz K.,
Marosi Gy., Szolnoki B.: Development of intumescent flame retardant for polypropylene: Bio-epoxy resin microencapsulated ammonium-polyphosphate. Periodica Polytechnica-Chemical Engineering,
66, 313-324 (2022)
10.3311/PPch.19468 IF=1.3 Q4
Mihályfi Á., Helmajer L., Lovas Z., Bordácsné Bocz, K., Ronkay F. Gy., Molnár B., Marosi Gy.: Thermoplastic polyester and its production. WO/2022/112807, Hungary (2022)
Bocz K.,
Ronkay F., Decsov K. E., Molnár B., Marosi Gy.: Application of low-grade recyclate to enhance reactive toughening of poly (ethylene terephthalate). Polymer Degradation and Stability,
185, 109505 (2021)
10.1016/j.polymdegradstab.2021.109505 IF=5.204 Q1
Ronkay F.,
Gere D.,
Czigány T.,
Molnár B.: Plastic waste from marine environment: Demonstration of possible routes for recycling by different manufacturing technologies. Waste Management,
119, 101-110 (2021)
10.1016/j.wasman.2020.09.029 IF=8.816 Q1
Bocz K.,
Ronkay F.,
Molnár B., Vadas D., Gyürkés M.,
Gere D.,
Marosi Gy.,
Czigány T.: Recycled PET foaming: supercritical carbon dioxide assisted extrusion with real-time quality monitoring. Advanced Industrial and Engineering Polymer Research,
4, 178-186 (2021)
10.1016/j.aiepr.2021.03.002Gere D.,
Ronkay F.,
Czigány T.: Investigation of the recyclability and compostability of biopolymers contaminated by petroleum-based polymers. Key Engineering Materials,
888, 23-28 (2021)
10.4028/www.scientific.net/KEM.888.23 Mihályfi Á., Helmajer L., Lovas Z., Bordácsné B. K., Ronkay F., Molnár B., Marosi G.: Hőre lágyuló poliészter és ennek előállítása.. P2000393, Hungary (2020)
Ronkay F., Molnár B., Nagy D., Szarka Gy., Iván B., Kristály F., Mertinger V., Bocz K.: Melting temperature versus crystallinity: new way for identification and analysis of multiple endotherms of poly(ethylene terephthalate). Journal of Polymer Research,
27, 372 (2020)/1-372 (2020)/17 (2020)
10.1007/s10965-020-02327-7 IF=3.097 Q2
Ronkay F., Molnár B., Szalay F., Nagy D., Bodzay B., Sajó I. E., Bocz K.: Development of Flame-Retarded Nanocomposites from Recycled PET Bottles for the Electronics Industry. Polymers,
11(2), 233, 233/1-233/19 (2019)
10.3390/polym11020233 IF=3.426 Q1
© 2014 BME Department of Polymer Engineering - Created by: Dr. Romhány Gábor