Development of special, weight-optimized rubber sealings for the vehicle industry
Project ID:
2019-1.1.1-PIACI-KFI-2019-00172
Supported by:
Hungarian National Research, Development and Innovation Office (NKFIH)
Term:
1 January 2020 - 31 December 2022
Supervisor (BME):
Dr. Tamás Bárány
Dr. Péter Tamás-Bényei
Participant researchers (BME):
Dr. Tamás Bárány
Dr. István Zoltán Halász-Kutasi
Dávid Zoltán Pirityi
Ákos Zoltán Halász
Dr. László Mészáros
Dániel Ábel Simon
Levente Ferenc Tóth
Dr. Péter Tamás-Bényei
Consortium partners (BME):
Tauril Kft. (konzorciumvezető)
Project summary
Transporting people and goods is a part of our everyday lives, so we use different vehicles every day. These vehicles can usually be described as very complex systems consisting of a huge number of parts, which must work well together. Many parts require that certain materials (engine oil, brake fluid etc.) are available at the right place and time and in the right amount. Sealings are widely used in the vehicle industry to prevent the leakage of these materials; most of these sealings are made from different kinds of rubber.
Nowadays much rubber sealing research and development is focused on high-performance rubber mixtures able to satisfy special requirements. With these high-performance mixtures the lifetime and reliability of rubber sealings can be improved, which can make transport safer. (Improved performance means the sealings can perform their function for a longer time and/or in more extreme conditions.)
The drive for such development is the increasing requirements in the vehicle industry because of continuous technological development. As a result, new materials and mixtures of new compositions are used. An excellent example is the ever increasing thermal load rubber sealings and gaskets have to withstand in addition to the load caused by aggressive materials (fuels, lubricants etc.), because of increasing performances of engines of decreasing size. Therefore, outstanding thermal stability and good resistance to aggressive materials (e.g. excellent resistance to oil and chemicals) even at high temperatures are essential requirements. These requirements can be satisfied with special rubber mixtures but their main component, the various special caoutchoucs are rather expensive, therefore mass reduction and optimization of the sealing is a very important area where costs can be decreased. As a result of structure optimization, the geometric characteristics of the product change, which changes the loads in the material of the product and so higher stresses and higher deformation occur when the cross section is decreased. In the case of rubber sealings and gaskets, this can reduce the functionality of the product if it is not “prepared” to take higher loads, which can be achieved by changing the components of the rubber mixture. If the components of the rubber mixture are properly chosen, or modified, the geometry of the product can be varied in a wider range because the mechanical properties of the rubber can be set to enable the product to provide sufficient sealing even at higher loads.
The goal of our project is to develop according to the above aspects the special rubber sealings the participating company manufactures for use in the vehicle industry, and rethink solutions currently used in industry practice in a mixture design-oriented way and with mass reduction in mind. The result will be technologies with which parts fully satisfying requirements but having lower manufacturing costs; As a result, the new technologies and the products manufactured with them will have a competitive advantage and they will likely be successfully used in other industries where sealings have to fulfil extreme requirements.
Project results
Section 1
1 January 2020 - 31 December 2020
In Section 1, we carried out research and development with Tauril Ltd. We carried out the identification of the requirements for the product to be manufactured and prepared a technical specification for the characteristics of the raw material. Detailed literature research was carried out in the field of special elastomeric materials, covering polychloroprene (CR), acrylonitrile-butadiene (NBR), hydrogenated acrylonitrile-butadiene copolymer (HNBR), fluor- and acrylate elastomers (ACM), and ethylene propylene diene monomer (EPDM) rubbers. The selection parameters for the different materials and types of seals were analyzed.
A wide range of tests (density measurement, Shore hardness measurement, tensile test, Soxhlet extraction test, Tg determination by DSC, thermal annealing, media resistance test in different fluids) were carried out to comprehensively characterize and qualify the experimental formulations created by Tauril Ltd. The studies included the recording and evaluation of the vulcanization curves of the raw mixtures, the vulcanization of the raw mixtures was carried out, and the vulcanizates were qualified. The results were used to propose the mixture to be used.
During the work phase, we purchased a Brabender Plasticorder Intermix internal mixer for the production of laboratory mixtures, which allowed us to produce more homogeneous mixtures with higher shear.
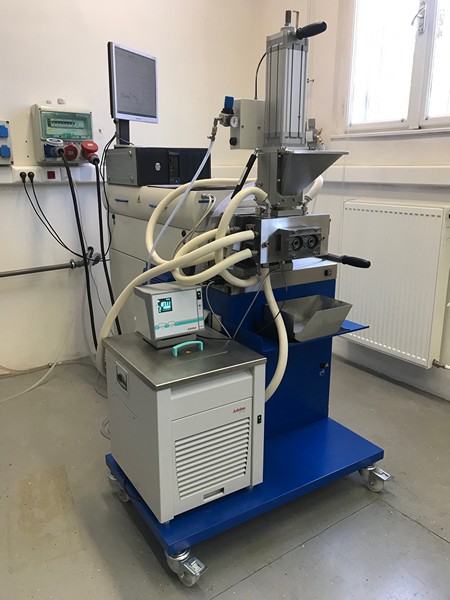
Brabender Plasticorder Intermix internal mixer
Section 2
1 January 2021 - 31 December 2021
In the second work phase, the substitutability of carbon black with white filler and the substitutability of EPDM rubber are investigated. Instead of EPDM we used NBR, which is able to meet the requirements for oil seals. Based on the literature review, a silica with medium activity was chosen as alternative filler. During the 2. section we analyzed the effects of plasticizers as well as coupling agents. The formulations of the developed carbon black-free recipe were mixed step by step using the Brabender Intermix 350 SX interpenetrating rotary laboratory internal mixer. Based on the literature review and the preliminary experiments, we chose a high-quality adipate ester as plasticizer, which has a beneficial effect even in the case of low-temperature processing, moreover, it improves flexibility and durability, as well as low migration and weather resistance. We analyzed the influence of coupling agent on the mechanical properties with a trimethoxysilane.
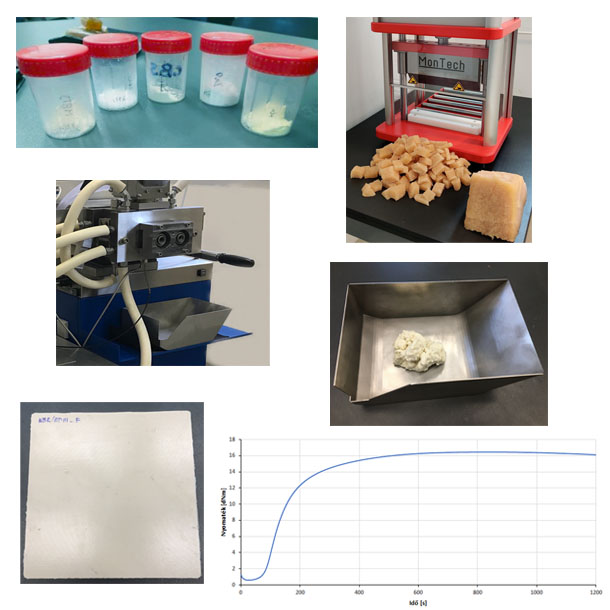
Development of carbon black-free mixtures
Section 3
1 January 2022 - 31 December 2022
During the third work phase, we carried out a literature review on alternative fillers that could potentially be used in the rubber industry, where the focus was on the carbon nanotubes and recycled carbon fibre.
We continued the research started in the second work phase, analysing the effect of plasticisers on the mechanical properties of vulcanisates, including density, thermal stability, compressive set and hardness changes under oil ageing. Using the formulations and experience gained in the second work phase, we created new formulations, replacing the previously used surface treatment agent (Silane M1-Trimethoxy) with a more efficient one (Bis(triethoxysilylpropyl)tetrasulfide). We evaluated the effect of the coupling agent on the vulcanizates basically through the studies described above for the softening effect, in addition to the change in mechanical properties. Beside the white filler, we analysed the effect of non-conventional fillers (milled carbon fibre and multiwall carbon nanotube) on the properties of rubber mixtures.
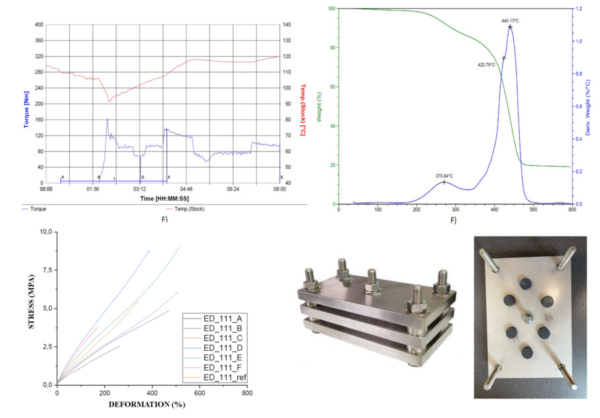
Analysis of the mixtures containing a plasticizer and a coupling agent
© 2014 BME Department of Polymer Engineering - Created by: Dr. Romhány Gábor