Development of multi-functional, high performance pseudo-ductile hybrid composites
Project ID:
FK 131882
Supported by:
Hungarian National Research, Development and Innovation Office (NKFIH)
Term:
1 December 2019 - 30 November 2023
Supervisor (BME):
Dr. Gergely Czél
Participant researchers (BME):
Salvatore Giacomo Marino
Dr. Kolos Molnár
Dr. Kornél Pölöskei
Dr. Gábor Romhány
Dr. Gábor Szebényi
Prof. Dr. Andrea Toldy
Project summary
One of the biggest challenges for the 21st century’s transportation sector is to improve fuel economy and reduce carbon footprint in case of traditional internal combustion engine driven vehicles. Since the energy storage elements of electric vehicles constitute a significant additional load, weight reduction is a key challenge for both constructions, while structural stiffness and passenger safety is to be maintained. High strength, low density yet safely failing structural materials could enable the development of the next economic and environmentally friendly generation of vehicles. High performance carbon or glass fibre reinforced polymer matrix composites offer exceptional specific modulus and strength, but suffer from sudden and brittle failure, with no warning and insufficient residual load-bearing capacity. Pseudo-ductile composites provide a safe alternative to conventional ones showing a progressive failure character and improved failure strains, similar to those of metals. Another significant benefit is a clear sign of damage before final failure. The principal investigator of the programme demonstrated pseudo-ductility in thin-ply uni- and multidirectional hybrid composites under tension recently. One objective of the project is the further development of the pseudo-ductile composites primarily by the modification of the layer interfaces. The other direction of the research is to add valuable functions such as damage indication and repairability which are of significant interest for safe operation and reduced lifecycle cost.
Project results
Section 1
1 December 2019 - 30 November 2020
Design, manufacturing and structural testing of a pseudo-ductile sandwich panel with additional visual overload sensing feature were completed according to the work plan. A 600x300x10 mm size panel with carbon fibre/epoxy composite skins and foam core was fabricated with a full layer of glass/epoxy-carbon/epoxy hybrid composite visual overload sensor integrated into the bottom skin. This rather large size was selected to demonstrate that the recently patented sensing technology is suitable for high performance, industrial-scale components. The sensing layer provided clearly visible signs of overload in the form of light stripes when the high modulus carbon reinforced sensing layer started to fragment and delaminated locally around the fractures at a pre-defined strain. 40 mm long electronic strain gauges were applied successfully and provided accurate strain reading over the highly variable strain field after the triggering of the overload sensing layer. The trigger strain of the visual overload sensor was in line with the expected failure strain of the sensing layer. Acoustic emission damage monitoring was able to detect the triggering of the visual overload sensor and the obtained data correlated well with the knee point after the initial linear part of the load-displacement diagrams and the small drops in the load signal from the test machine indicating the fragmentation of the sensing layer.
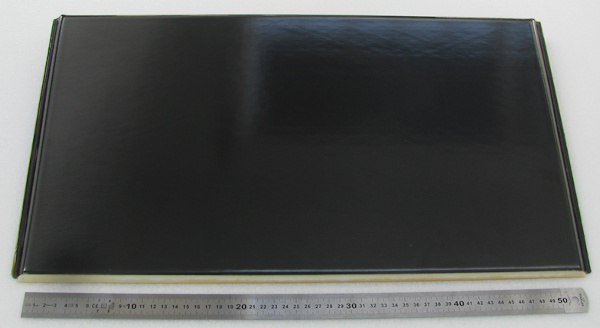
Pseudo-ductile, self-monitoring sandwich panel
Section 2
1 December 2020 - 30 November 2021
According to the work plan, the main task of the second period of the programme was to modify the layer interfaces of our hybrid composites to make them pseudo-ductile, improve their performance and extend the scope of the new materials. Successful experimental programme was designed and executed using (30 and 60 um thick) thermoset resin films and thermoplastic acrylonitrile butadiene styrene (ABS) films at the layer interfaces to increase the mode II interlaminar fracture toughness and stabilise the delamination in the hybrid laminates made with standard thickness carbon/epoxy layers sandwiched between glass/epoxy layers. Excellent results were achieved with another thermoplastic film: polyamide 12 (PA 12) which was not applied in film format before as an interleaf layer for toughening laminated composites. The hybrid laminate specimens, which failed with unstable delamination without the PA 12 film interleaves demonstrated favourable pseudo-ductile behaviour with 20 um PA 12 films at the glass/epoxy-carbon/epoxy layer interfaces. The carbon/epoxy layer fragmented with no visible delamination even at 3% strain, where the tests were stopped to prevent final failure. An additional interface modification approach was applied successfully to the layer interfaces of our hybrid laminates to make their failure pseudo-ductile. Electrospun nanofibrous layers made of polyamide 6 (PA 6) with two different concentrations were used as interleaf layers in different areal densities ranging from 2 to 20 g/m2 between the carbon/epoxy and the glass/epoxy composite layers of our hybrid laminates. The interleaved nanofibrous layers helped to control the thickness of a well-defined interlayer between the composite block with thicknesses in correlation with the areal densities of the applied interleaves. Interface modification led to significant increase in the mode II interfacial fracture toughness of our samples.
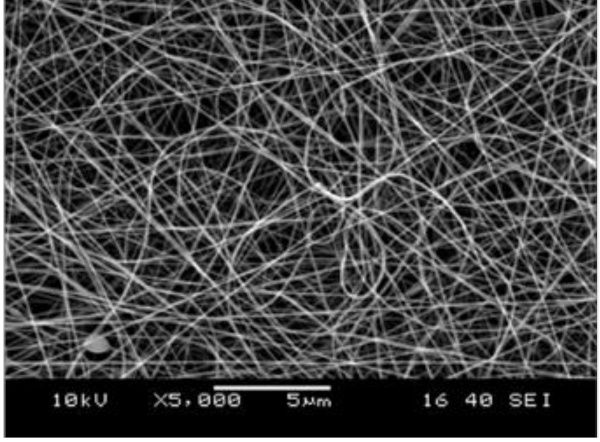
Scanning electron micrograph of an electrospun polyamide veil suitable for interfacial toughening
Section 3
1 December 2021 - 30 November 2022
According to the work plan, the main task of the third period of the programme was the development of pseudo-ductile, repairable composite materials. Three layer unidirectional hybrid composites were made from prepregs in autoclave with glass fibre/epoxy and carbon fibre/epoxy layers including 20 um thick PA12 films at the layer interfaces. The carbon-epoxy layer was cut to 50 mm long strips before laying up the hybrid laminates. This way the fracture of the carbon fibre epoxy layer was avoided and only delamination took place upon tensile loading of the specimens. The material demonstrated a desirable non-linear pseudo-ductile stress-strain response with smooth transitions between the initial linear, the slightly rising plateau and the second linear phases. The careful control of the damage mode of the material (i.e. no fibre breakage) allowed us to restore the initial stiffness of the specimens, after 30-40% loss due to delamination, by repairing the specimens under heat and pressure. The damaged specimens were placed in our autoclave at a temperature just above the melt temperature of the PA 12 films inside and 7 bar pressure for only 10 minutes. As a result, the delamination visible from the outside of the specimens due to the translucent nature of the outer glass fibre/epoxy layers disappeared. At the same time, the stiffness of the specimen was fully restored to that of the pristine samples, right until the strain and stress corresponding to the limit of linear stress-strain response (i.e. knee point).
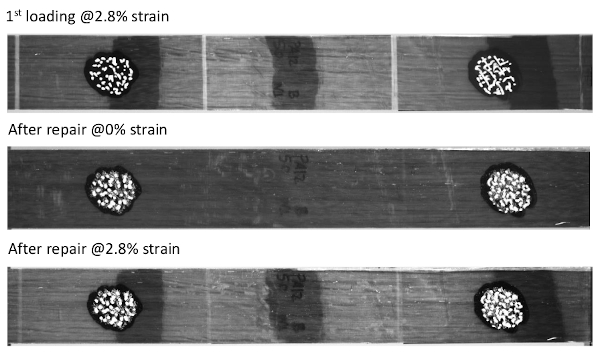
Pseudo-ductile, repairable hybrid composite coupon after damage introduction, after repair, after re-loading
Section 4
1 December 2022 - 30 November 2023
According to the work plan, the main task of the fourth period of the programme was the damage tolerance characterisation of the developed materials subjected to out-of-plane loading. We designed 4 mm thick quasi-isotropic laminates with and without interfacial modification at the mid-plane of the laminates where the highest shear stress is expected during out of plane indentation. The scope of the study was to analyse the extent of the damage introduced in the 100x150 mm test panels by the penetration of a 16 mm diameter hemispherical indenter until a given displacement. Glass fibre/epoxy material was used since it is transparent and can potentially show damage evolution inside the laminate if sufficiently strong backlight is applied. We inserted a 40 mm diameter release film piece in the middle of the panels which acted as an interfacial weakening element to control the onset of damage and localise delamination initiation to the modified area. This could be a successful strategy to minimise delamination at other interfaces and keep two thick blocks of the laminate intact which can take higher load in the subsequent compression after indentation test than a laminate which contains damage at multiple interfaces. Indentation tests were executed while the damage evolution was recorded with a digital camera originally supplied with our video-extensometer. Certain differences between the baseline and modified test panels in the damage accumulation patterns were identified, but further tests are necessary to draw conclusions. During the first compression after indentation tests, we experienced the expected correlation between the extent of introduced damage and the compressive strength of the panels and also the effect of lay-up sequence.
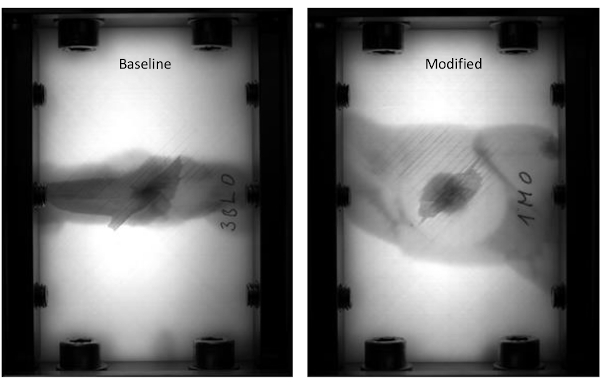
Damage patterns developed during compression after indentation test
Section 5
1 December 2023 - 31 May 2024
Project-related publications
Suwarta P., Wisnom M. R., Fotouhi M., Wu X.,
Czél G.: Pseudo-ductile compressive behaviour of unidirectional thin-ply carbon /glass fibre-epoxy hybrid composites. Composites Part A: Applied Science and Manufacturing,
195, 108877/1-108877/15 (2025)
10.1016/j.compositesa.2025.108877 IF=8.1 Q1
Wisnom M.R., Pimenta S., Shaffer M.S.P., Robinson P., Potter K.D., Hamerton I.,
Czél G., Jalalvand M., Fotouhi M., Anthony D.B., Yu H., Longana M.L., Wu X., Bismarck A.: High performance ductile and pseudo-ductile polymer matrix composites: A review. Composites Part A: Applied Science and Manufacturing,
181, 108029/1-108029/39 (2024)
10.1016/j.compositesa.2024.108029 IF=8.1 Q1
Czél G.: Direct comparison of novel unidirectional sandwich coupon designs for accurate tensile failure strain determination of carbon fibre epoxy material. in 'ECCM21 – 21st European Conference on Composite Materials Nantes, Franciaország . 2024.07.02.-05.,Vol 4. 25-32 (2024)
Czél G.: Development of sandwich test coupons with continuous protective layers for accurate determination of the tensile failure strain of unidirectional carbon fibre reinforced composites. Composites Part A: Applied Science and Manufacturing,
187, 108440/1-108440/12 (2024)
10.1016/j.compositesa.2024.108440 IF=8.1 Q1
Marino S. G.,
Czél G. : Development and characterisation of reparable, film-interleaved, pseudo-ductile hybrid composites. Composites Part A: Applied Science and Manufacturing,
169, 107496/1-107496/13 (2023)
10.1016/j.compositesa.2023.107496 IF=8.1 Q1
Czél G. , Bugár-Mészáros M., Wisnom M. R.: Combined effect of moisture and test temperature on the pseudo-ductility of thin-ply carbon/epoxy-glass/epoxy hybrid composites. Composites Part A: Applied Science and Manufacturing,
165, 107353/1-107353/11 (2023)
10.1016/j.compositesa.2022.107353 IF=8.1 Q1
Marino S. G., Kuželová Košťáková E. ,
Czél G. : Development of pseudo-ductile interlayer hybrid composites of standard thickness plies by interleaving polyamide 6 nanofibrous layers. Composites Science and Technology,
234, 109924/1-109924/14 (2023)
10.1016/j.compscitech.2023.109924 IF=8.3 Q1
Marton G. Zs., Mezey Z., Czél G.: Prepregből autoklávban gyártott kompozit lemezek rétegközi tulajdonságainak alakulása a térhálósítás során alkalmazott technológiai paraméterek függvényében. in 'XXXI. Nemzetközi Gépészeti Konferencia (OGÉT 2023) Temesvár, Románia. 2023.04.27-2023.04.30.,354-359 (2023)
Rev T., Wisnom M. R., Xu X.,
Czél G. : The effect of transverse compressive stresses on tensile failure of carbon fibre/epoxy composites. Composites Part A: Applied Science and Manufacturing,
156, 106894/1-106894/9 (2022)
10.1016/j.compositesa.2022.106894 IF=8.7 Q1
Czél G. : Development of bi-directional pseudo-ductile glass/carbon-epoxy hybrid composites for improved safety in structural applications. Composites Part B: Engineering,
231, 109546/1-109546/9 (2022)
10.1016/j.compositesb.2021.109546 IF=13.1 D1
Marino S. G.,
Czél G.: Improving the performance of pseudo-ductile hybrid composites by film-interleaving. Composites Part A: Applied Science and Manufacturing,
142, 106233/1-106233/16 (2021)
10.1016/j.compositesa.2020.106233 IF=9.463 Q1
He H.,
Molnár K.: Fabrication of 3D printed nanocomposites with electrospun nanofiber interleaves. Additive Manufacturing,
46, 102030/1-102030/11 (2021)
10.1016/j.addma.2021.102030 IF=11.632 D1
He H., Guo J., Illés B., Géczy A., Istók B.,
Hliva V.,
Török D.,
Kovács J. G., Harmati I.,
Molnár K.: Monitoring multi-respiratory indices via a smart nanofibrous mask filter based on a triboelectric nanogenerator. Nano Energy,
89, 106418/1-106418/12 (2021)
10.1016/j.nanoen.2021.106418 IF=19.069 D1
Kara Y.,
He H.,
Molnár K.: Shear‐aided high‐throughput electrospinning: A needleless method with enhanced jet formation. Journal of Applied Polymer Science,
137, e49104/1-e49104/13 (2020)
10.1002/app.49104 IF=3.125 Q2
Marino S.G., Mayer F., Bismarck A.,
Czél G.: Effect of plasma-treatment of interleaved thermoplastic films on delamination in interlayer fibre hybrid composite laminates. Polymers,
12, 2834/1-2834/24 (2020)
10.3390/polym12122834 IF=4.329 Q1
He H., Gao M.,
Török D.,
Molnár K.: Self-feeding electrospinning method based on the Weissenberg effect. Polymer,
190, 122247/1-122247/9 (2020)
10.1016/j.polymer.2020.122247 IF=4.43 Q1
He H., Wang Y., Farkas B., Nagy Zs. K.,
Molnár K.: Analysis and prediction of the diameter and orientation of AC electrospun nanofibers by response surface methodology. Materials & Design,
194, 108902/1-108902/11 (2020)
10.1016/j.matdes.2020.108902 IF=7.991 Q1
He H., Gao M., Illés B.,
Molnár K.: 3D Printed and Electrospun, Transparent, Hierarchical Polylactic Acid Mask Nanoporous Filter. International Journal of Bioprinting,
194, 108902/1-108902/11 (2020)
10.18063/ijb.v6i4.278 IF=6.638 Q1
Wisnom M., Potter K., Czél G., Jalalvand M.: Strain overload sensor. GB2544792B, United Kingdom (2020)
© 2014 BME Department of Polymer Engineering - Created by: Dr. Romhány Gábor