Novel thermoplastic dynamic vulcanizates (TDV) with enhanced wear resistance based on in situ produced polyurethane matrix
Project ID:
K 128268
Supported by:
Hungarian National Research, Development and Innovation Office (NKFIH)
Term:
1 December 2018 - 31 August 2023
Supervisor (BME):
Dr. Tamás Bárány
Participant researchers (BME):
Dr. István Zoltán Halász-Kutasi
Andrea Zelenainé Kohári
Project summary
To find a potential solution for the recycling of used rubber products is a key issue of environmental protection. One of the viable opportunities is the replacement of several traditional crosslinked rubbers with alternative materials that have matching overall performance and properties, but can be recycled more simply and economically. One of the emerging family of materials showing rubber-like behavior is the group of so-called thermoplastic dynamic vulcanizates (TDVs). These TDVs, composed of a continuous thermoplastic phase in which rubber is finely dispersed, combine the beneficial properties of its components, namely the elastic behavior of rubbers and the simple, processing (and also possible reprocessing) of plastics. Accordingly, manufacturing TDVs with properties similar to those of traditional rubbers could be a straightforward solution to the above-mentioned problem. However, the overall performance of TDVs can be limited by the inadequate adhesion between the rubber and the thermoplastic phase. Our intention is to enhance this bonding with a new reactive production technique, involving the in situ synthesis of the thermoplastic phase (PU), which should improve interfacial adhesion, partly due to the mutual entanglement of the molecules of each phase. This should yield a strong interphase between the rubber and the thermoplastic phase and thus lead to an improvement in the overall performance of the in situ produced blend. A further aim of this project is to investigate the effects of recycling this novel TDV and determine the effects of repeated processing on its properties.
Project results
Section 1
1 December 2018 - 30 November 2019
We reviewed the literature in the field and collected the relevant initial knowledge for the research. Based on the literature, the raw materials for the synthesis of thermoplastic polyurethane (TPU) were selected and obtained.
Within the project a Bruker Tensor II type FTIR spectrometer was purchased, so that the investigation of the material structure properties relevant for the research could be carried out in-house.
The synthesis was carried out in an internal mixer, using production parameters and formulations based on literature data, and the effect on the properties of the TPUs was investigated. In our work, we investigated the applicability of two polyols, polytetrahydrofuran and hydroxyl-terminated polybutadiene, and in the case of polytetrahydrofuran, the effect of the ratio of polyol to chain extender on the properties of the final polyurethane. By increasing the ratio of polyol, the prepared thermoplastic polyurethane can be softened and its hardness can be reduced. The investigation of the applicability of hydroxyl-terminated polybutadiene was important because the TPUs so produced may be able to form better bonds with polybutadiene or polybutadiene copolymer-based rubbers in the manufacture of thermoplastic dynamic vulcanizates (TDVs). Among manufacturing parameters, the effects of mixing time and different rotor speeds were also explored.
The development of the other component of TDVs, the rubber phase, was initiated in the pursuit of formulation simplicity, with only vulcanizing agents being added to the NBR, XNBR and ENR rubbers chosen as models. The starting rubbers are polar in nature, similar to the thermoplastic polyurethane phase, which is the basis for the cooperation of the two phases. These rubber compounds were also qualified and used to produce TDVs using the experience gained from polyurethane synthesis.
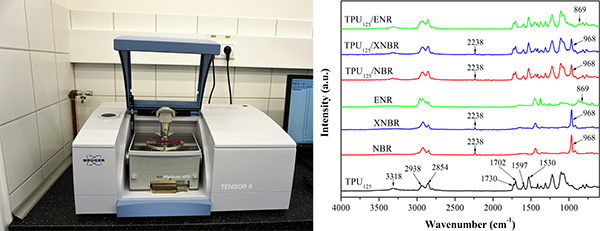
Bruker Tensor II type Fourier transform infrared spectrometer and spectras of the samples
Section 2
1 December 2019 - 30 November 2020
The work started by investigating the reproducibility of thermoplastic polyurethane synthesis. By comparing the torque and temperature curves recorded by the internal mixer of TPUs prepared at different times under the same conditions and formulation, we found that they are different. This is important because the change in torque is a good indicator of the change in molecular weight if all other parameters are unchanged. When examining the mechanical properties of the samples, we also found significant differences.
Due to their hydrophilic nature, the materials used for synthesis are susceptible to water absorption, and the water they contain can react with the diisocyanate, leading to adverse side reactions. The chain extender used is able to bind the moisture content of the air entering the glass, which cannot be completely expelled by vacuum drying or other simpler drying methods. To overcome this problem, 1,4-butanediol was poured into smaller glass bottles under inert atmosphere and zeolite was added to it to absorb possible tiny amounts of water. These glass bottles are stored in a desiccator containing phosphorus pentoxide.
To produce thermoplastic polyurethanes, we have also experimented with the two-step or also known as prepolymer method in addition to the one-step method used previously. One of the advantages of this process is that it is less harmful to health and is therefore becoming more widespread in industry. Another is that it allows polyurethane with a much more regular structure to be produced. We used four prepolymers with different isocyanate contents. %). In addition to the 1,4-butanediol chain extender, we tried 1,6-hexanediol as well. We performed different tests on the TPU samples produced. As the isocyanate content of the prepolymer increased, the samples became stiffer and their tensile strength increased, while their elongation at break decreased. Furthermore, by using 1,6-hexanediol, we obtained better results for the same prepolymer.
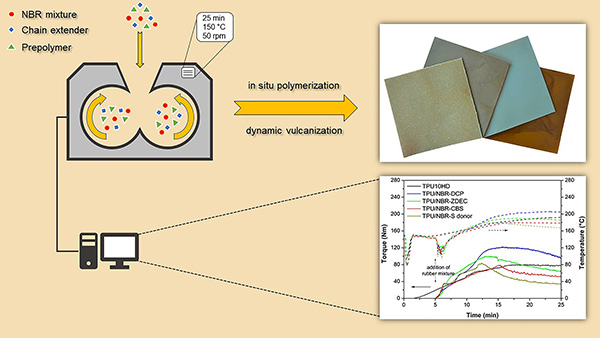
Preparation of thermoplastic polyurethane-based thermoplastic elastomers by the prepolymer method
Section 3
1 December 2020 - 30 November 2021
Thermoplastic dynamic vulcanizates (TDVs) with thermoplastic polyurethane (TPU) matrix were prepared in an internal mixer. TPU was synthesized by the prepolymer method using the previously selected prepolymer and chain extender. As the dispersed phase, acrylonitrile butadiene rubber (NBR)-based blends containing peroxide and sulfur vulcanization systems with different accelerators were used. The results of the tests showed that dicumyl peroxide is able to form chemical bonds not only in the rubber phase but also between the two phases, thus improving the mechanical properties of TDVs. Among the rubber mixtures containing different sulfur vulcanization systems, the one with the longest scorch time achieved the best results. This allowed the rubber phase to be fragmented and evenly distributed in the matrix before vulcanization started.
We then worked on improving the compatibility of the TPU matrix and the rubber phase by different methods. The feasibility of in situ production of matrix TPU was also investigated. The results clearly show the beneficial effect on compatibility, as both the tensile strength and elongation at break of the samples were increased. The effect of the polarity of the NBR used was also analyzed. The experiment was carried out with different acrylonitrile (AN) rubbers. It was shown that the mechanical properties of the TDVs at room temperature are not significantly affected by the acrylonitrile content of the NBR. However, the dynamic mechanical analysis showed that the cold resistance of the resulting TDVs deteriorated with increasing the AN content of the rubber phase. In addition, the effect of different vinyl acetate contents on the properties of ethylene-vinyl acetate (EVA) copolymers was investigated. The mechanical properties of the TDVs deteriorated under the influence of EVA. SEM images of the cryo-fractured surface of the samples showed that EVA appeared as a third phase in the TDVs, which weakened them as an additional defect site
Section 4
1 December 2021 - 30 November 2022
In the spirit of the circular economy, we have turned our attention to the use of recycled materials to develop thermoplastic vulcanizates with a thermoplastic polyurethane (TPU) matrix. Worldwide, approximately 1.5 billion scrap tires are generated each year, containing more than 40 wt% of various synthetic and natural rubber components. They can be recycled as a regrind from which the various reinforcing structures have been removed. It is believed that the rubber regrind recovered in this way could partially or completely replace the rubbers used in the rubber phase of our dynamic vulcanizates.
Building on our previous results, we have thermomechanically devulcanized the ground tire rubber (GTR) produced from truck tire treads by high-pressure water jet milling using a twin-screw extruder.
TPU-based blends were prepared with ground tire rubber (GTR) and devulcanized ground tire rubber (dGTR). In the experiment, the GTR and dGTR content of the blends was varied between 0 and 50 wt% and the effect of the composition on their mechanical properties was investigated.
Compounding was performed on a twin-screw extruder, followed by injection molding to produce sheet samples. With a view to a possible future industrial application, it is important to emphasize that both the compounding and the injection molding of the specimens were easy to perform, even with a 50 wt% filler content. It was found that the tensile strength, stiffness and Shore A hardness of the samples decreased with increasing the amount of the rubber phase. In contrast, the elongation at break of our samples increased slightly at 10 wt% rubber content. However, even at 50 wt% GTR content, the elongation at break of our samples was higher than 300%. It was also shown that devulcanization of the GTR resulted in a better relationship between the two phases.
Section 5
1 December 2022 - 31 August 2023
In the last phase of the work, we looked for alternatives to replace the ground tire rubber (GTR) produced by water jet milling. Keeping in mind the future exploitation of the results and the possible commercialization of thermoplastic dynamic vulcanizates (TDV) based on the current research, we decided to use a devulcanized ground tire rubber (dGTR), which is available on the market and can be easily obtained in large quantities.
In our work, we varied the content of thermoplastic polyurethane (TPU)-based blends of GTR and dGTR (0, 30, 40, 50 and 60 wt%) and studied the effect of the composition on their mechanical properties. In addition, an attempt was made to dynamically vulcanize dGTR during compounding to produce TDVs.
In our preliminary experiments, we found that the induction time (t10) of dGTR-based rubber compounds is extremely short at the temperature used to prepare TDVs. Therefore, a formulation development was performed prior to dynamic vulcanization. Different vulcanization systems based on sulfur, peroxide and resin were used and the vulcanization and mechanical properties of the blends were investigated.
The results obtained were used to select a sulfur- and a peroxide-based system for the vulcanization of the rubber phase. The rubber compound for TDVs was prepared in an internal mixer, the compounding was performed in a twin-screw extruder, and sheet specimens were prepared by injection molding.
Comparing the effects of GTR and dGTR, dGTR softened the compounds by up to 40 wt%, reducing their strength and modulus while increasing their elongation at break. This is in contrast to the results for samples containing 50 and 60 wt% dGTR. In these cases, a double continuous structure could be formed first, and as the dGTR content was further increased, the devulcanizate became the continuous phase. This may also explain why TDVs containing 60 wt% dGTR could not be produced.
Project-related publications
Görbe Á.,
Kohári A.,
Bárány T.: Rubber compounds from devulcanized ground tire rubber: Recipe formulation and characterization. Polymers,
16, 00455/1-00455/19 (2024)
10.3390/polym16040455 IF=4.7 Q1
Görbe Á.,
Kohári A.,
Halász-Kutasi I.,
Bárány T.: Thermomechanical-chemical devulcanization of ground tire rubber. IOP Conference Series: Materials Science and Engineering,
1313, 012008/1-012008/10 (2024)
10.1088/1757-899X/1313/1/012008 Kohári A.,
Bárány T.: Sustainable thermoplastic elastomers based on thermoplastic polyurethane and ground tire rubber. Journal of Applied Polymer Science,
141, e56157/1-e56157/10 (2024)
10.1002/app.56157 IF=2.7 Q2
Pirityi D. Z.,
Bárány T.,
Pölöskei K.: Recycling of EPDM rubber via thermomechanical devulcanization: Batch and continuous operations. Polymer Degradation and Stability,
230, 111014/1-111014/9 (2024)
10.1016/j.polymdegradstab.2024.111014 IF=6.3 D1
Kiss L.,
Mészáros L.: Recycling waste tire rubber through an innovative water-medium ionizing radiation treatment: Enhancing compatibility and mechanical performance. Radiation Physics and Chemistry,
216, 111475/1-111475/8 (2024)
10.1016/j.radphyschem.2023.111475 IF=2.8 Q1
Simon D. Á.,
Bárány T.: Microwave devulcanization of ground tire rubber and its improved utilization in natural rubber compounds. ACS Sustainable Chemistry & Engineering,
11, 1797-1808 (2023)
10.1021/acssuschemeng.2c05984 IF=7.1 Q1
Kohári A., Bárány T.: Termoplasztikus poliuretán alapú elasztomer fejlesztése újrahasznosított gumiőrlet társításával. Műanyag- és Gumiipari Évkönyv, 21, 94-98 (2023)
Kiss L.,
Simon D. Á.,
Bárány T.,
Mészáros L.: Synergistic effects of gamma pre-irradiation and additional vulcanizing agent in case of ground tire rubber containing vulcanizates. Radiation Physics and Chemistry,
201, 110414/1-110414/7 (2022)
10.1016/j.radphyschem.2022.110414 IF=2.9 D1
Kohári A.,
Bárány T.: Development of thermoplastic vulcanizates based on in situ synthesized thermoplastic polyurethane and acrylonitrile-butadiene rubber: the influence of the curing system. Journal of Polymer Research,
29, 361/1-361/12 (2022)
10.1007/s10965-022-03176-2 IF=2.8 Q3
Kohári A.,
Bárány T.: In situ–produced polyurethane-based thermoplastic elastomers: the effect of the acrylonitrile content of the rubber phase. IOP Conference Series: Materials Science and Engineering,
1246, 012001/1-012001/8 (2022)
10.1088/1757-899X/1246/1/012001 Kohári A., Halász I. Z., Bárány T.: In situ előállított, poliuretán alapú termoplasztikus elasztomerek fejlesztése. Polimerek, 5, 622-625 (2019)
Kohári A.,
Halász I. Z.,
Bárány T.: Thermoplastic dynamic vulcanizates with in situ synthesized segmented polyurethane matrix. Polymers,
11, 1663/1-1663/1-15 (2019)
10.3390/polym11101663 IF=3.426 Q1
© 2014 BME Department of Polymer Engineering - Created by: Dr. Romhány Gábor